5 Potential Screen Printing Problems & How To Solve Them
Introduction:
In this article we will explore five common screen printing problems that screen printers encounter and provide detailed solutions to overcome them. By understanding these issues and implementing the suggested remedies, you can enhance the quality of your screen print screen and achieve more consistent and professional screen printing painting results.
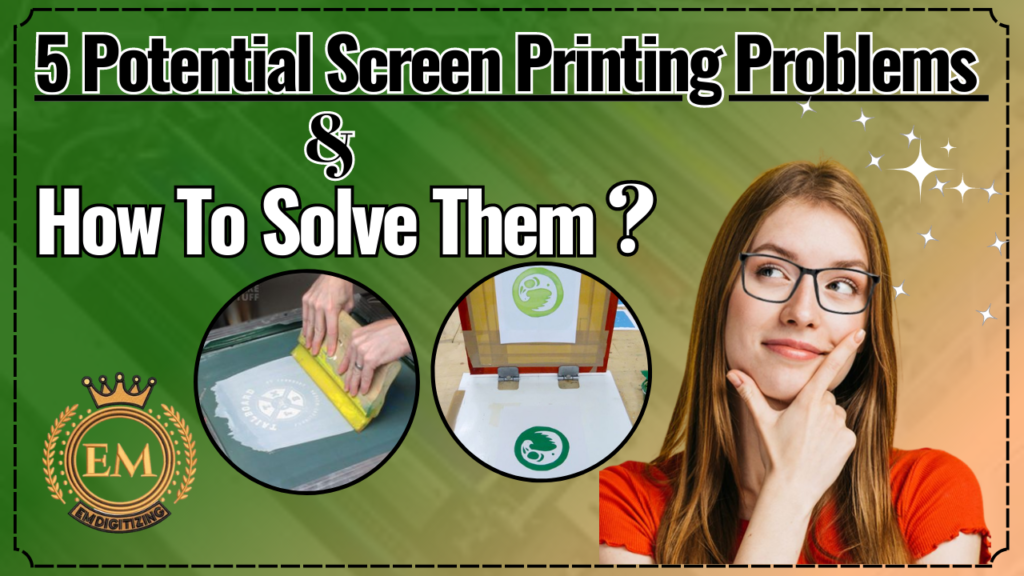
5 Potential Screen Printing Problems & How To Solve Them
What Is A Screenprint?
Let’s see how does sublimation work and how to avoid sublimation on dark colors mistakes.
Screen printing on fabric is a versatile and popular method for creating high-quality prints on various surfaces. However, like any printing technique, screen printing process is not without its challenges.
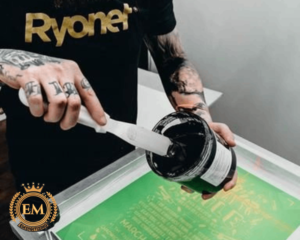
5 Potential Screen Printing Problems & How To Solve Them
Let’s discuss 5 potential screen silk printing problems and see how to solve them:
Problem 1: Ink Bleeding
Ink bleeding refers to the undesired spreading of ink, causing fuzzy or blurred prints by exceeding the intended boundaries. It can be caused by factors such as excessive ink application, improper screen thread tension, or inadequate squeegee pressure.
To prevent ink bleeding, ensure proper screen painting tension and use the appropriate mesh count for the design. Apply the right amount of pressure while printing, and consider using a low-bleed ink or adding a bleed-blocking agent to the ink mixture. Test prints and adjust variables as needed.
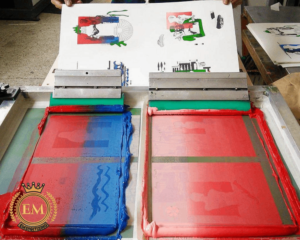
Problem 2: Misprints and Mistakes
Screen printing mistakes can be frustrating, but they can be rectified with the right techniques. When mistakes occur, act promptly. For misprints, remove the garment from the press and replace it with a new one. If the mistake is on the screen, clean it thoroughly before proceeding. Take measures to improve registration, such as using registration guides or ensuring accurate stencil alignment.
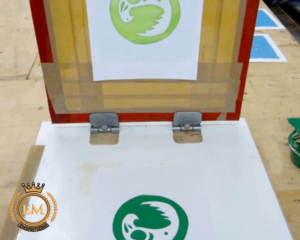
Problem 3: Poor Ink Adhesion
Having ink adhere properly to the substrate is crucial for durable and long-lasting prints. Factors like improper screen preparation, insufficient ink curing, or unsuitable substrate choice can lead to adhesion issues.
To solve this problem, make sure to degrease and properly coat the screen printing with emulsion. Verify that the ink is suitable for the chosen fabric or substrate. Experiment with different ink additives or adhesion promoters to improve ink adhesion.
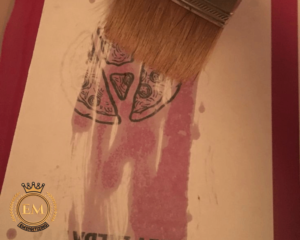
Problem 4: Pinholes
Pinholes are tiny voids in the printed image that can negatively impact the overall quality of the print. They are often caused by contaminants on the screen or improper emulsion coating. To solve this issue, clean the screen thoroughly before each print run, ensuring no contaminants are present. If pinholes persist, consider increasing the exposure time during stencil exposure to ensure proper curing.
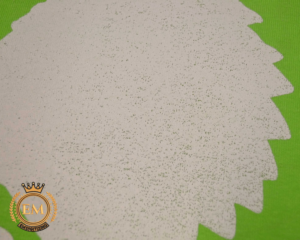
Problem 5: Registration Challenges
Registration challenges in paint for screen print refer to difficulties in aligning multiple colors or layers accurately during the screen printing process. To address these challenges, ensure stable screens by maintaining proper tension. Use registration marks or templates as guides for alignment. Invest in quality equipment with micro-registration capabilities. Practice proper setup and preparation to improve registration accuracy.
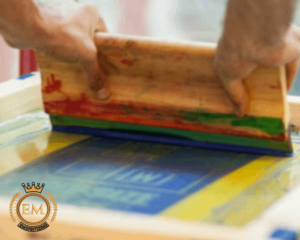
Tips To Help You With Screen Printing:
Here are some tips to help you with screen printing:
- Ensure that your screen printmaking is clean and free from any residue or debris before applying emulsion. This will help prevent issues like pinholes and uneven coating.
- Invest in quality screens, inks, and emulsions. Using reliable and reputable products can significantly improve the overall designing for screen printing experience and the quality of your prints.
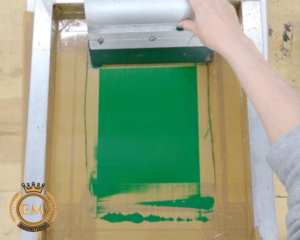
- Before starting a full production run, always perform test prints to check for any potential issues or adjustments needed. This will allow you to make necessary modifications before committing to larger quantities.
- Apply consistent and even pressure when pulling the squeegee across the screen. Inconsistent pressure can result in uneven ink deposits and affect the overall print quality.
- A clean and organized workspace is essential for efficient and accurate printing. Regularly clean your equipment, screens, and work surface to prevent contamination or stray ink from affecting your prints.
- Follow the manufacturer’s recommendations for drying or curing your prints. Improper drying or curing can lead to issues such as smudging or poor ink adhesion.
- Don’t hesitate to reach out to experienced screen printers or join online communities and forums to seek advice and learn from others’ experiences. Sharing knowledge and insights can greatly enhance your skills as a screen printer.
- Regularly check and adjust the tension of your screens to ensure consistent and accurate prints. Loose screens can result in misregistration or smudging, while overly tight screens can lead to premature screen breakdown.
- Screen printing can be challenging, but don’t get discouraged. Keep practicing, experimenting, and refining your techniques. With time and perseverance, you will become more proficient and achieve the desired results.
- If you’re using custom-mixed inks or adjusting colors, make sure to mix them thoroughly and perform test prints to ensure the desired color and consistency before starting a full production run.
- Invest in a quality screen tension meter to accurately measure and adjust the tension of your screens. Proper tensioning helps achieve precise registration and consistent ink transfer.
- Fluctuations in temperature and humidity can impact the screen printing process. Aim to work in a stable environment with controlled temperature and humidity levels to minimize variables that could affect ink drying, emulsion exposure, and overall print quality.
- Different embroidery designs and substrates may require different mesh counts. Experiment with various mesh counts to find the optimal one for your specific print job. Higher mesh counts are typically used for finer details, while lower mesh counts are suitable for bold and thicker prints.
- Ensure your stencils are properly aligned on the screens. Invest in registration guides or use alignment marks to achieve accurate placement of your design layers and minimize misregistration issues.
- When printing multiple copies of the same design, maintain a consistent print speed throughout the process. Consistency in speed helps ensure uniform ink deposition and color saturation across all prints.
- To prolong the life of your screens, clean them thoroughly right after each printing session. Promptly remove excess ink, emulsion, or any residue to prevent clogging or buildup that could affect future prints.
- Experiment with different squeegee angles, pressures, and strokes to find the optimal combination for your specific prints. Pay attention to achieving smooth, even strokes to ensure consistent ink coverage.
- Establish a systematic workflow for your screen printing process. This includes steps such as screen preparation, stencil application, ink mixing, registration, printing, and clean-up. Having a well-defined workflow helps streamline your process and maintain consistency.
- Stay curious and open to learning new techniques, exploring different materials, and experimenting with innovative approaches. Attend workshops, read books, watch tutorials, and engage with the screen printing community to stay up-to-date with the latest trends and advancements.
Remember, mastering how to make screen prints, how does screen printing work, and screen printing itself takes time and practice. By implementing these tips and continuously honing your skills, you’ll be well on your way to producing high-quality screen prints.
Conclusion:
Screen printing in art can present various challenges, but armed with the right knowledge and solutions, these issues can be overcome. By addressing screening painting problems such as ink bleeding, misprints, poor ink adhesion, pinholes, and registration challenges, you can elevate the quality of your screen prints. Implementing the recommended techniques and paying attention to detail throughout the printing process will help you achieve consistent and professional results. With practice and experience, you will become adept at troubleshooting and producing exceptional screen prints that meet your artistic or commercial objectives.
If you are in need of personalized embroidery logo digitization, look no further than EM DIGITIZING. We specialize in providing top-notch services for customizing embroidery logos, ensuring exceptional quality. Take advantage of our exclusive offer of a 50% discount on all our services for new customers. Request a complimentary quote today, and our team will promptly assist you.
Thank you for taking the time to read!
Bleeding in screen printing can be caused by excessive ink application, improper screen tension, or inadequate squeegee pressure. Adjusting these factors and using proper ink consistency can help minimize bleeding.
To fix screen printing mistakes, identify the issue (e.g., smudges, misalignment), let the ink dry completely, and then use appropriate techniques like spot cleaning, touch-ups, or reprinting with careful registration to correct the errors.
Ink sticks to the screen in screen printing due to the mesh openings and capillary action. When the screen is properly prepared, coated, and dried, the ink adheres to the exposed areas, resulting in a desired print.
Pinholes in screen printing can be prevented by using a higher mesh count screen, ensuring proper emulsion coating and drying, using appropriate squeegee pressure, and maintaining clean screens free from debris.
Screen printing can be challenging due to factors like achieving precise designs registration, managing ink consistency and drying, troubleshooting issues like bleeding or misprints, and mastering the technique of applying even pressure while controlling variables like mesh tension and squeegee angle. Practice, experience, and attention to detail can help overcome these difficulties.