Top 8 Types of Screen Printing Process In 2023
Introduction:
Screen printing has long been a popular method for transferring designs onto various surfaces, from textiles to paper and plastics. As technology advances, new screen printing processes emerge, offering enhanced capabilities and efficiency. In this article, we will delve into the top different 8 types of screen printing processes that are making waves in 2023, showcasing their unique features and applications.
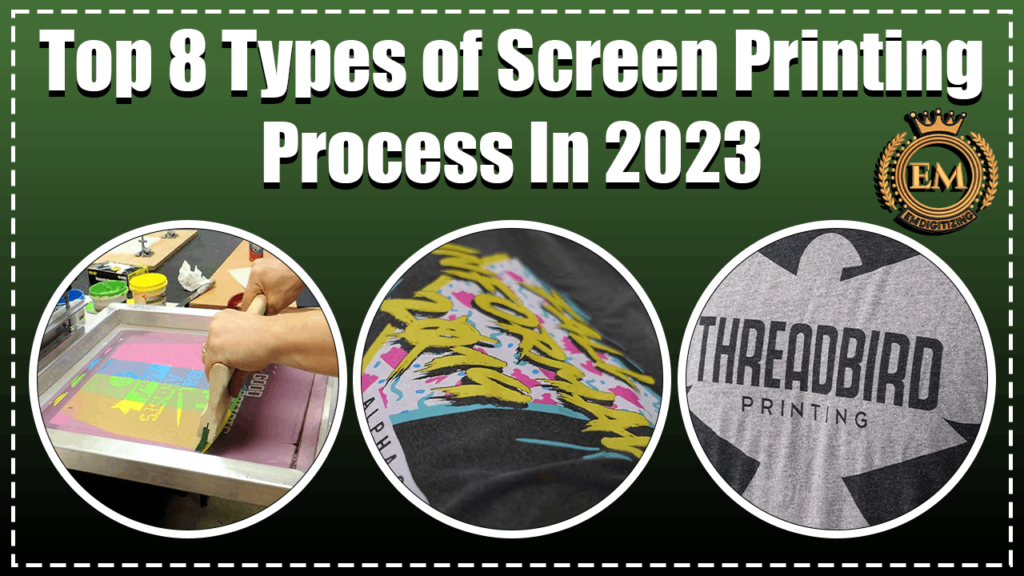
Top 8 Types of Screen Printing Process In 2023
8 Types of Screen Printing Processes In 2023
Let’s see the top 8 screen print types processes in 2023:
Traditional Screen Printing:
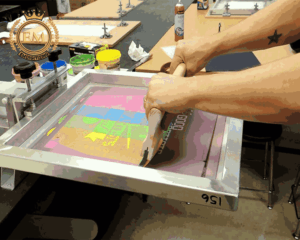
Also known as flatbed screen printing, this is the classic method that involves a mesh screen, a stencil, and a squeegee. Ink is pushed through the stencil onto the substrate, creating the desired design. Traditional screen printing in art remains a reliable choice for large-scale production and offers excellent color vibrancy and durability.
Water-Based Screen Printing
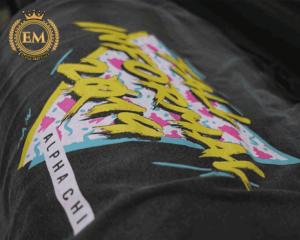
Water-based screen printing utilizes water-based inks instead of traditional solvent-based inks. This method offers several advantages, including eco-friendliness, soft and breathable prints, and the ability to achieve a wide range of colors. Water-based screen printing methods are particularly popular in the fashion industry, where sustainability and comfort are highly valued.
Discharge Screen Printing:
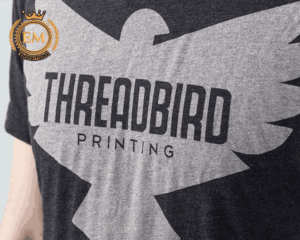
Discharge screen printing involves using a specialized ink that removes the dye from the fabric, resulting in a bleached effect. This technique is commonly used on dark-colored garments and produces soft, vintage-like prints. Discharge printing techniques offers a unique aesthetic appeal and is favored in the fashion and streetwear industries.
Plastisol Screen Printing:
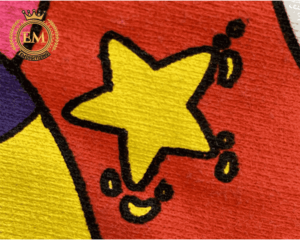
Plastisol screen printing employs a thick, plastic-based ink that sits on top of the fabric rather than penetrating it. This types of printing in art method is known for its vibrant colors, opacity, and longevity. Plastisol prints retain their vividness and durability even after numerous washes, making them suitable for apparel, promotional items, and outdoor signage.
Simulated Process Screen Printing:
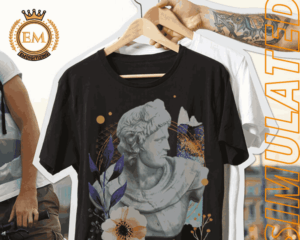
Simulated process screen printing is specifically designed for reproducing highly detailed, photorealistic images with a wide range of colors. By utilizing halftones and blending techniques, this method achieves smooth gradients and subtle shades. It is often used for printing on T-shirts, posters, and other merchandise requiring high-quality image replication.
High-Density Screen Printing:
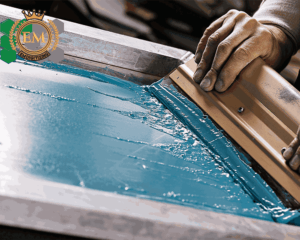
High-density screen printing creates raised or textured effects by applying a thick layer of ink to the substrate. This types of art printing technique adds depth and dimension to the design, resulting in a tactile and visually appealing outcome. High-density prints are popular in sportswear, branding, and promotional products.
Foil Screen Printing:
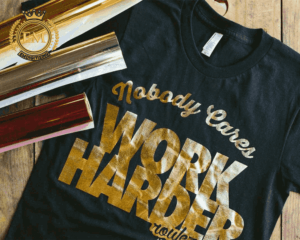
Foil screen printing involves applying a layer of metallic foil onto the embroidery design, creating a shiny, reflective effect. The foil is transferred using heat and pressure, resulting in a striking and luxurious finish. Foil screen printing ideas are commonly used for adding accents, logos, or embellishments to high-end apparel, invitations, and packaging.
All-Over Screen Printing:
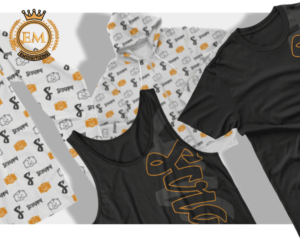
All-over screen printing, also known as jumbo screen printing, allows for printing across the entire surface of a garment or substrate. This method utilizes oversized screens and specialized equipment to achieve seamless and continuous designs. All-over printing is particularly popular in the fashion industry for creating bold and eye-catching apparel.
Tips To Improve Your Screen Printing Process
Here are some tips to improve your screen printing process:
Ensure that your artwork is high-quality, properly sized, and optimized for screen printing. Use vector graphics or high-resolution images to achieve sharp and crisp prints.
The screen mesh determines the level of detail you can achieve. Select a mesh count appropriate for your design. Higher mesh counts are ideal for intricate designs, while lower mesh counts are suitable for bold and larger designs.
Coat your screens evenly with emulsion and allow them to dry in a controlled environment. Follow the recommended exposure times to achieve the desired level of stencil hardness.
Invest in high-quality inks that are formulated specifically for screen printing. Consider using additives like extenders or reducers to achieve the desired ink consistency and performance.
Ensure that your ink is properly mixed and has the right consistency. Too thick or too thin ink can lead to printing issues. Test your ink on scrap fabric before starting the production run.
Regularly check and calibrate your printing equipment, including the screen tension, squeegee pressure, and off-contact distance. Properly maintained equipment ensures consistent and accurate prints.
Before printing on the final product, conduct test prints to check for any potential issues or adjustments needed. Perform quality control checks throughout the production run to maintain consistency and identify any defects.
Follow the manufacturer’s guidelines for curing the prints. Ensure that the ink is fully cured to achieve maximum durability and wash resistance. Use proper curing equipment, such as a heat press or conveyor dryer, to achieve consistent and reliable results.
Clean your screens and tools after each use to prevent ink buildup and clogging. Proper maintenance extends the lifespan of your screens and ensures consistent print quality.
Don’t be afraid to experiment with different techniques, inks, and substrates. Learn from your printing experiences, make adjustments as needed, and continue to refine your process.
Ensure your printing area is clean and free from dust or debris that could affect the print quality. Properly align and secure your screens on the printing press to ensure accurate registration. Use registration marks or a registration system to achieve precise alignment between colors or layers.
Take time to properly mix and match your ink colors to achieve the desired shades and tones. Keep a record of your ink mixing ratios for consistent color reproduction in future print runs. Perform color tests and adjustments as necessary to achieve accurate color matching.
Use the appropriate squeegee hardness for your specific ink and substrate combination. Apply consistent and even pressure during the printing stroke to ensure smooth ink coverage. Maintain a proper angle and speed while printing to avoid ink smearing or uneven application.
Explore the use of specialty inks such as metallics, fluorescents, or glow-in-the-dark inks to add unique visual elements to your prints. Consider incorporating special effects like high-density printing, foil applications, or textured finishes to create eye-catching and tactile designs.
Allow sufficient drying time for your prints before handling or curing to prevent smudging or ink transfer. Follow the recommended curing instructions for your specific ink type to ensure optimal durability and wash resistance. Properly store and handle finished prints to avoid damage or color fading over time.
Stay updated with the latest advancements and techniques in screen printing through workshops, online tutorials, or industry publications. Seek feedback from experienced printers or mentors to identify areas for improvement and implement best practices. Practice regularly to refine your skills and experiment with new ideas to push the boundaries of your screen printing capabilities.
By implementing these tips, you can enhance the quality and efficiency of your screen printing process. Remember, practice and continuous improvement are key to mastering the art of screen printing.
Conclusion:
As technology evolves, the world of silk screen techniques continues to expand and diversify. The top 8 types of screen printing processes outlined in this article offer a glimpse into the exciting possibilities and applications in 2023. Whether it’s traditional screen printing for mass production or specialized techniques like water-based printing for sustainability, screen printing remains a versatile and powerful method for transferring designs onto various surfaces. With advancements in ink formulations, equipment, and design software, screen printing continues to push boundaries and inspire creativity in industries ranging from fashion to advertising.
Looking for top-notch customization of embroidery logo digitizing? Look no further than EM DIGITIZING! We specialize in delivering the highest quality embroidery logo digitizing services. Plus, we have an exclusive offer for our first-time customers – enjoy a whopping 50% off on all our services. Get a free quote today and let us bring your vision to life! If you have any queries or comments, don’t hesitate to reach out. Thank you for taking the time to read this article!
Screen printing uses the technique of forcing ink through a stencil onto a substrate using a mesh screen. It is a versatile and widely used printing method for various materials.
The most popular printing method currently is DTG (Direct-to-Garment) printing. It allows for high-quality, full-color prints directly onto garments, offering flexibility and intricate details.
When it comes to longevity, screen printing is known for its durability. The ink used in screen printing forms a strong bond with the fabric design, making it highly resistant to fading or cracking over time.
The latest printing technology in the industry is UV printing. It utilizes ultraviolet light to instantly cure the ink, allowing for printing on a wide range of surfaces and providing vibrant colors, sharp details, and quick drying times.
DTF (Direct-to-Film) printing is a relatively new technology that offers cost advantages over traditional screen printing methods. It eliminates the need for screens and reduces setup time, making it potentially more cost-effective for certain applications.