Do you know what sets weaving and machine embroidery apart in the textile universe?
Weaving is the classic process of interlacing threads to construct fabrics from scratch—essentially, it’s how raw yarns are transformed into cloth.
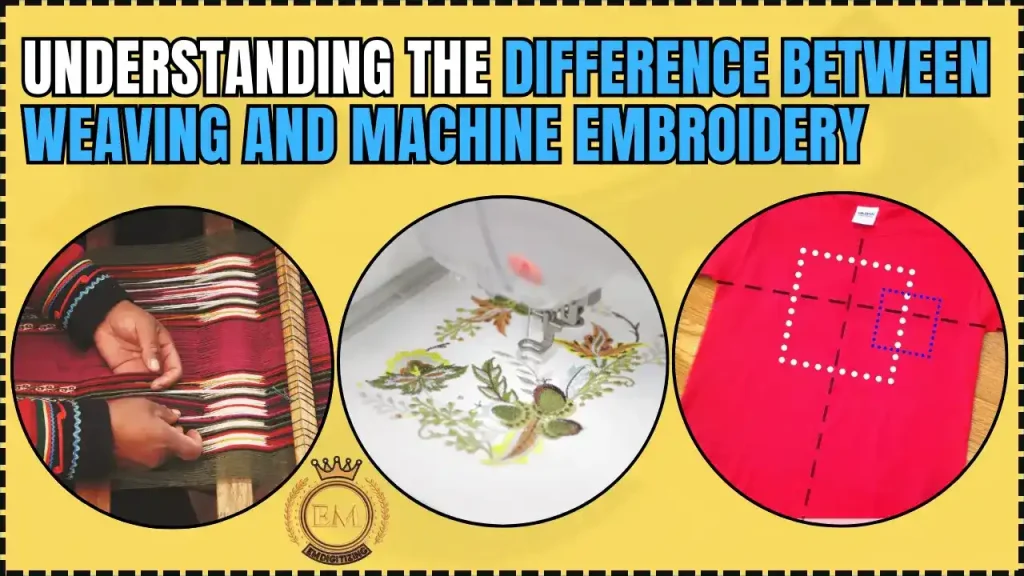
Meanwhile, machine embroidery involves stitching intricate patterns onto existing fabric, elevating it with decorative and colorful designs. These techniques shape the world of textiles in unique ways, contributing to everything from sturdy canvas to delicate embroidered linens.
Let’s delve into the distinctive characteristics and applications of each to understand their impact on our everyday textiles.
Understanding the Difference Between Weaving and Machine Embroidery
What is Weaving?
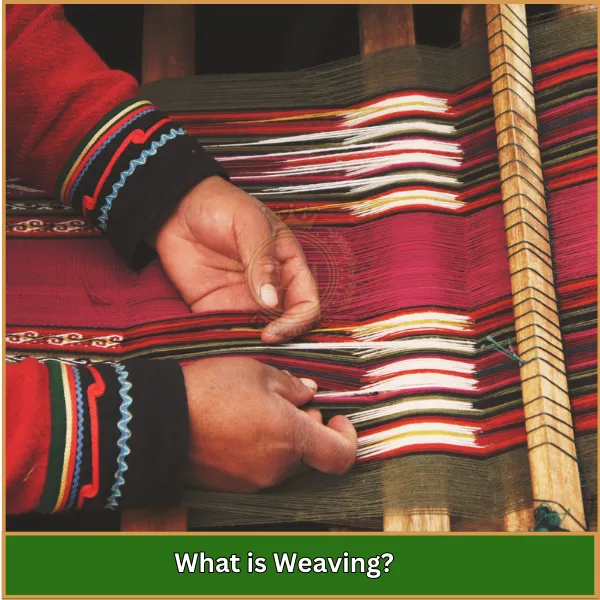
Weaving is a textile production method that involves interlacing two sets of threads—warp (longitudinal) and weft (lateral)—at right angles to create fabric. This process typically takes place on a device called a loom.
Types of Weaving
There are several types of weaving, each with its own characteristics and uses.
1. Plain Weave
- Threads alternate over and under each other.
- Examples: Muslin, chiffon.
- Characteristics: Durable and flat surface.
2. Twill Weave
- Creates a diagonal pattern by passing the weft over and under multiple warp threads.
- Examples: Denim, houndstooth.
- Characteristics: Strong and wrinkle-resistant.
3. Satin Weave
- Multiple weft threads pass over fewer warp threads, resulting in a glossy surface.
- Examples: Satin, sateen.
- Characteristics: Luxurious feel, less durable.
4. Basket Weave
- Uses pairs of yarns in both directions for a checkerboard pattern.
- Characteristics: Often used in upholstery.
5. Jacquard Weave
- Creates intricate patterns using a special loom.
Examples: Brocade, damask.
6. Leno or Gauze Weave
- Pairs of warp threads twist around each other for an open fabric.
Characteristics: Lightweight and airy.
Advantages and Disadvantages of Weaving
It has been used for centuries to create fabrics, and like any technique, it has its own set of advantages and disadvantages depending on the material and purpose.
Advantages
- Durability
- Variety of Textures
- Cost-Effective for Bulk Production
Disadvantages
- Limited Design Complexity
- Time-Consuming Setup
- Requires Skilled Labor
What is Machine Embroidery?
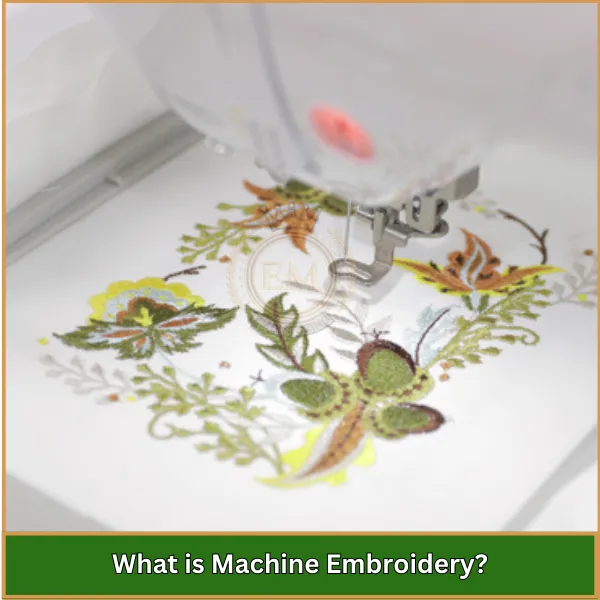
It is a method of decorating fabric using a sewing machine or a specialized embroidery machine to create intricate patterns and designs.
This technique allows for high precision and consistency, making it popular in both commercial and personal applications.
It can be used for branding, decorative purposes, and creating personalized items.
Types of Machine Embroidery
There are various types of machine embroidery, each suited for different applications and needs.
1. Free-Motion Machine Embroidery
- Utilizes a standard zigzag sewing machine.
- The operator manually moves the fabric under the needle to create designs.
- Each design is unique and cannot be easily reproduced.
2. Computerized Machine Embroidery
- Involves machines that are controlled by a computer.
- Designs are pre-programmed and can be executed automatically.
- Eliminates the need for manual rethreading for multi-color designs.
3. Single Head Embroidery Machine
- Designed for smaller production runs.
- Features one head that can embroider one item at a time.
- Ideal for custom pieces or small orders.
4. Multi-Head Embroidery Machine
- Contains multiple heads, allowing simultaneous embroidery on several items.
- Efficient for bulk production while maintaining quality.
5. Schiffli Embroidery Machine
- Uses multiple needles that penetrate the fabric simultaneously.
- Commonly employed for producing intricate designs on lace and similar textiles.
6. Cornely Hand-Guided Embroidery
- Requires an operator to guide the machine manually.
- Produces special stitches like chain stitch and satin stitch, often used in interior design applications.
Advantages and Disadvantages of Machine Embroidery
It is a fast and precise way to add designs to fabric, but it also has its own set of pros and cons depending on the tools and techniques used.
Advantages
- High Precision and Consistency
- Speed
- Versatility in Design
Disadvantages
- Higher Initial Costs
- Less Personal Touch
- Complexity in Programming
Difference Between Weaving and Machine Embroidery
Weaving and Machine Embroidery have different roles in the textile industry, with each using its own methods and results. Here are the main differences:
- Production Technique
- Purpose
- Equipment Used
- Material Flexibility
- Design Placement
- Skill Set
- End Product
- Pattern Complexity
- Production Speed
- Customization
1. Production Technique
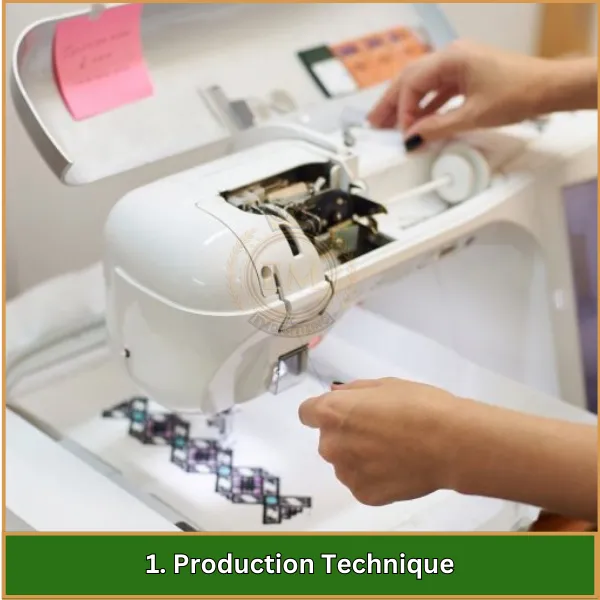
Weaving and Machine Embroidery: Weaving involves interlacing two sets of yarns or threads at right angles to each other to create fabric.
This method relies on a loom and the process can produce textiles ranging from simple cotton fabrics to complex tapestries.
Embroidery, on the other hand, involves using a needle and thread to add decorative stitches to a fabric base, often after the fabric has been woven.
2. Purpose
Weaving serves the primary purpose of creating fabric from threads or yarns. Embroidery is used to embellish fabric with patterns or images, enhancing the aesthetic and sometimes the functional value of the material with additional color, texture, and design.
3. Equipment Used
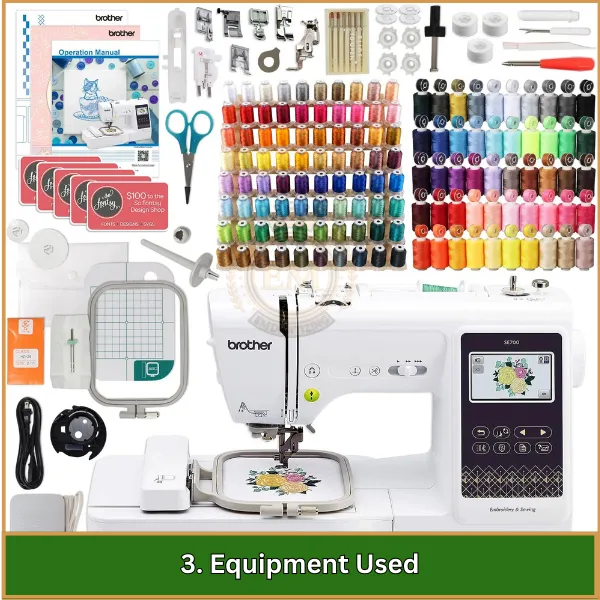
The main equipment for Weaving and Embroidery includes looms for weaving, which can be either simple hand-operated frames or complex automated machines.
Embroidery uses specialized machines that can handle multiple threads and colors, designed to apply intricate designs onto fabric.
4. Material Flexibility
Weaving typically uses materials such as yarns made of cotton, wool, silk, or synthetic fibers designed to form durable fabrics. Embroidery materials include not only traditional threads but also specialty threads like metallics, silks, and those used in bead embroidery and bead weaving to add texture and decorative details.
5. Design Placement
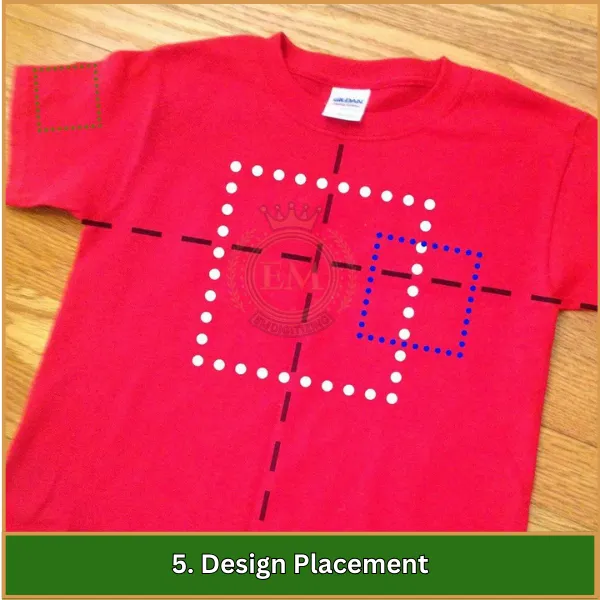
In weaving, design elements must be planned and integrated into the fabric as it is being created on the loom. Embroidery allows for design application post-fabric production, providing flexibility to add personalized and detailed artwork anywhere on the existing material.
6. Skill Set
Weaving requires an understanding of the loom’s mechanics, as well as the ability to set up patterns and manage the tension and interlacing of threads. Embroidery demands skills in design digitization, machine setup, and the handling of various stitching techniques to achieve desired artistic effects.
7. End Product
The products of weaving are textiles that form the building blocks of other products, such as garments and home furnishings. Embroidered items often represent finished goods themselves, featuring enhanced visual appeal with decorated surfaces.
8. Pattern Complexity
Pattern complexity in weaving is limited by the capabilities of the loom and can be geometric and repetitive. Embroidery offers a broader range of possibilities, enabling highly detailed and elaborate designs that can include varying stitch patterns, gradients, and image-like complexity.
9. Production Speed
Weaving can produce large quantities of fabric relatively quickly, especially with modern automated looms. Embroidery, especially detailed work, is more time-consuming, focusing on meticulous detail over speed, making it less efficient for large-scale fabric production but ideal for bespoke and artisanal creations.
10. Customization
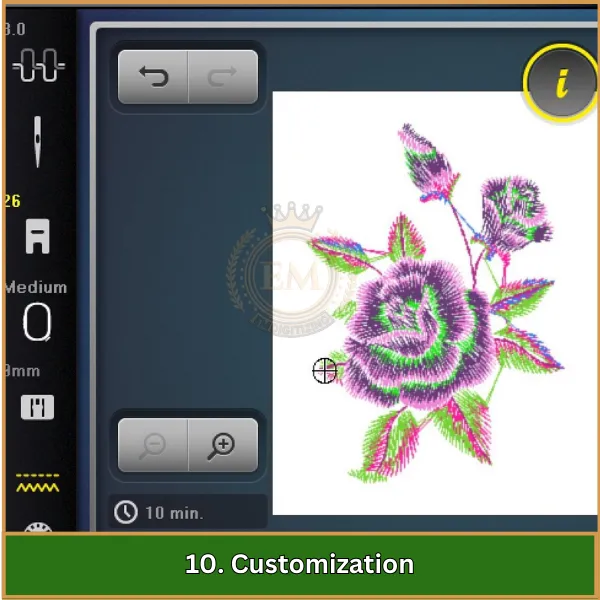
Weaving offers limited customization options which depend largely on the loom setup and the yarns used. Embroidery provides extensive opportunities for customization, allowing for a wide range of colors, designs, and personal touches to be added to any fabric after it has been woven.
Deciding Between Weaving and Machine Embroidery for Your Projects
When deciding between these techniques for your textile projects, consider the following points:
Purpose of the Project:
- Use weaving if you need to create fabric from the ground up—ideal for making textiles with specific characteristics like thickness, durability, and texture.
- Choose machine embroidery if you’re looking to add decorative details to existing fabric, perfect for personalized designs or branding.
Project Requirements:
- Weaving allows you to tailor the foundational aspects of your fabric, suitable for applications that require custom material creation.
- Machine embroidery enhances and embellishes fabric with colorful, intricate patterns, ideal for artistic projects or commercial branding.
Understanding what each process offers will help you make the best choice for your specific needs, whether you’re creating new fabric or enhancing the existing one with beautiful embroidery.
Final Words
With a clear understanding of weaving and machine embroidery, it’s easy to see how embroidery adds a special touch to any fabric. If you’re looking to add custom designs to your project, EMDigitizing can make that process simple.
We offer high-quality digitizing services that transform your artwork into ready-to-stitch embroidery files. Our services are fast, reliable, and affordable.
Plus, as a new customer, you’ll get an incredible 50% off your first order! Get started with EMDigitizing and watch your designs come to life effortlessly.
FAQs
Stitching refers to using a needle and thread to join fabric pieces together or to create decorative designs on fabric. Weaving, on the other hand, is the process of interlacing two sets of threads, the warp and weft, at right angles to form a fabric.
There are two main types of machine embroidery: free-motion embroidery, where the user manually controls the stitching on a basic sewing machine, and computerized embroidery, which automatically stitches digitized designs using a specialized embroidery machine.
Weaving is the process of making fabric by interlocking two distinct sets of yarns or threads, called the warp and the weft, on a loom.
Machine embroidery is a method of creating patterns on fabric using a sewing or embroidery machine. The designs are pre-programmed into the machine, which stitches them automatically onto the fabric.