T-shirt screen printing is a popular and versatile method for creating custom designs on fabric.
Whether you’re a small business owner looking to promote your brand or an individual wanting to express your creativity, mastering the art of screen printing can open up a world of possibilities.
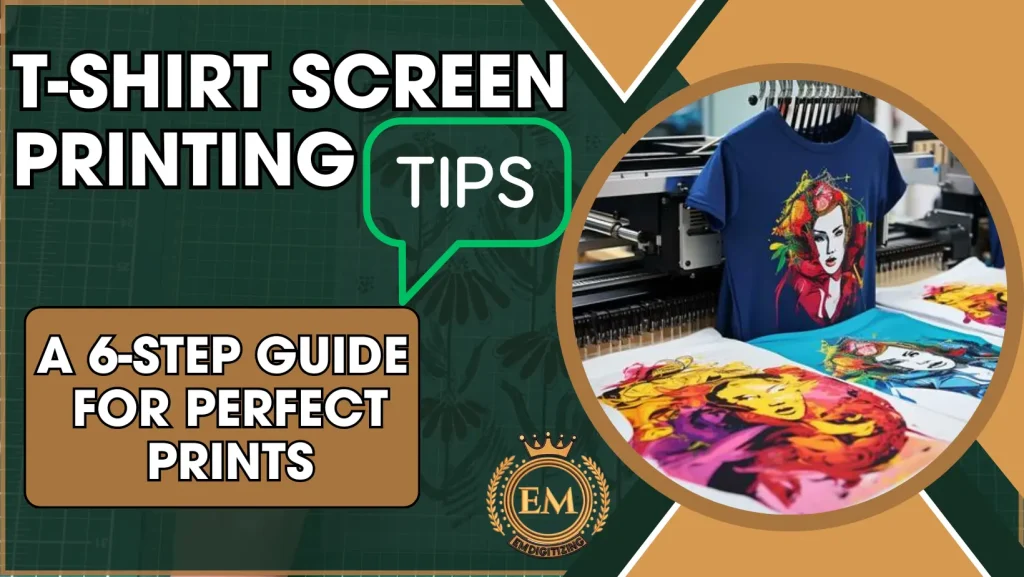
This comprehensive guide will walk you through the six essential steps to achieve perfect prints every time.
T-Shirt Screen Printing Tips: 6-Step Guide for Perfect Prints
From selecting the right equipment and materials to troubleshooting common issues, we’ll cover everything you need to know to become a proficient t-shirt screen-printer.
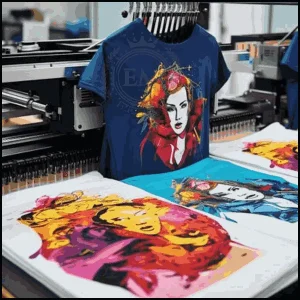
So, let’s dive in and explore the fascinating world of t-shirt screen printing together.
What is T-Shirt Screen Printing?
T-shirt screen printing is a popular method of applying designs onto fabric using screens and ink. It involves creating a stencil on a screen, through which ink is forced to create the desired design on the t-shirt.
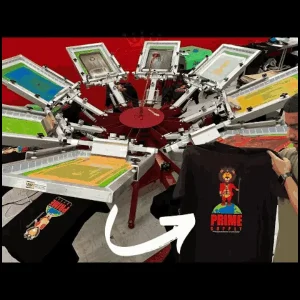
Advantages of T-Shirt Screen Printing
Screen printing offers several advantages for t-shirt printing. Firstly, it allows for vibrant and long-lasting prints that won’t fade away after a few washes.
Secondly, it provides great flexibility in terms of design and color options, allowing you to bring your creative ideas to life.
Lastly, screen printing can be cost-effective for larger quantities, making it an excellent choice for events, businesses, or promotional purposes.
Essential Equipment and Materials
Essential equipment and materials form the backbone of any task or project, ensuring that operations run smoothly and efficiently.
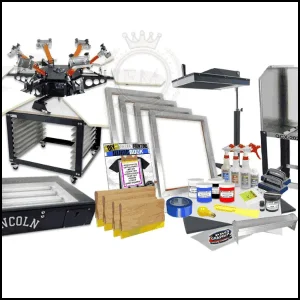
Screen Printing Press
A screen printing press is the backbone of your printing setup. It holds the screen in place and enables consistent pressure during the printing process.
Screens and Mesh Counts
Screens with various mesh counts are used to create different levels of detail in your prints. Higher mesh counts are ideal for intricate designs, while lower mesh counts work better for bold, solid designs.
Inks and Additives
When it comes to inks, there are countless options available. Water-based inks are popular for their soft feel and eco-friendliness, while plastisol inks are known for their vibrant colors and durability.

Additives, such as extenders or reducers, can help you achieve specific effects or improve the ink’s flow.
Squeegees and Emulsion Coaters
Squeegees are used to push the ink through the screen and onto the t-shirt. Different squeegee durometers (hardness) are available, allowing you to choose the one that suits your printing needs.
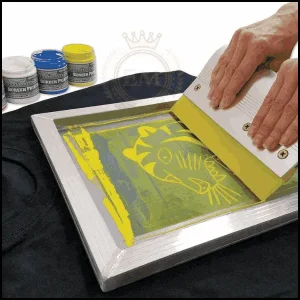
Emulsion coaters, on the other hand, are used to evenly apply the emulsion onto the screen, creating the stencil.
Preparing the Artwork and Design
Preparing the artwork and design is a critical phase in the creative process, where ideas and concepts are translated into visual representations.
Design Considerations for Screen Printing
When designing for screen printing, keep in mind that each color requires a separate screen. Therefore, it’s important to simplify your design and minimize the number of colors to avoid complexity and increase efficiency.
Vectorizing and Preparing the Artwork
To ensure smooth printing, convert your design into a vector format and clean up any imperfections. This will help create clean, crisp lines and prevent any unexpected surprises during the printing process.
Color Separation
For multi-colored designs, color separation is essential. This process involves separating each color into individual layers, allowing you to create separate screens for each color and print them one by one.
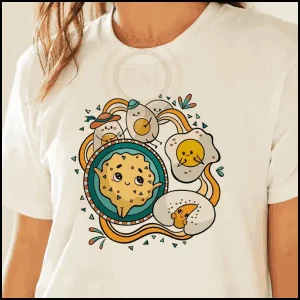
Preparing the Screen and Ink
Preparing the screen and ink is a vital step in the screen printing process, where precision meets creativity.
Choosing the Right Screen
Selecting the right screen is crucial for achieving accurate and precise prints. Consider the mesh count, screen size, and frame material based on your design and desired outcome.
Applying Emulsion and Creating Stencils
Coating your screen with emulsion and creating the stencil is a vital step in the screen printing process. Follow the manufacturer’s instructions to evenly apply the emulsion, ensuring proper exposure and thorough rinsing to reveal the desired stencil.
Mixing and Preparing the Ink
Mixing ink colors accurately is essential to achieve the desired shades and tones. Mixing cups, scales, and Pantone color guides can help you achieve consistent and accurate color matching.
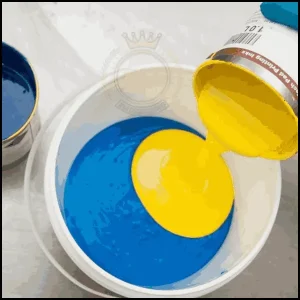
Step-by-Step Printing Process
The step-by-step printing process is a methodical approach to transferring designs onto a variety of materials, requiring attention to detail and mastery of technique.
Setting up the Screen on the Press
Before you dive into the exciting world of screen printing, you need to set up your screen on the press. It’s like preparing the canvas before you paint your masterpiece.
Make sure the screen is tightly secured on the press, so it doesn’t wiggle around like a drunk jellyfish. A stable screen will give you crisp and clean prints.
Aligning the Design and Platen
Now that your screen is ready, it’s time to align your design with the platen. Think of it as a high-stakes game of connect-the-dots but with more ink.
Take your time to ensure the design is centered on the platen, or else you might end up with a T-shirt that looks like it was printed by a blindfolded monkey.
Proper Ink Application Techniques
The moment has arrived to unleash your inner Picasso and apply the ink. Don’t be stingy with it, but don’t go wild either.
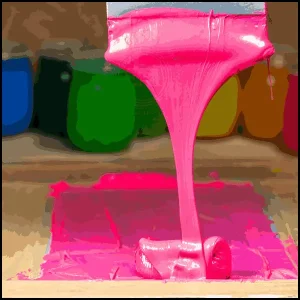
Use just enough ink to make your design stand out, like a peacock flaunting its feathers. It’s all about finding that sweet spot between too little and too much ink.
Spread it evenly across the screen, like a smooth criminal.
Curing and Drying the Printed Shirts
Congratulations, you’ve successfully printed your shirts! But don’t celebrate just yet, because they need some tender loving care to reach their full potential. Curing and drying the prints is like sending them to a luxurious spa retreat.
Follow the instructions for the specific ink you’re using and give those shirts a nice heat treatment to ensure the prints stay vibrant and last longer.
Troubleshooting Common Printing Issues
Ah, the joy of troubleshooting. Just when you thought everything was going smoothly, a wild printing issue appears. Don’t panic!
Here are some common problems you may encounter and how to tackle them:
- Ink Bleeding: If your ink is spreading outside the lines like a rebellious teenager, try using less pressure when applying the ink or switch to a thicker ink consistency. You can also try using a lower mesh screen to prevent ink from seeping through.
- Uneven Prints: If your design looks like a Picasso masterpiece (but not in a good way), double-check that your screen is properly aligned with the shirt. Uneven pressure or an improperly stretched screen can also cause this issue.
- Ink Smudges: If your print looks like it was attacked by a mischievous ink monster, there may be excess ink on the screen, or your squeegee could be too dirty. Clean both thoroughly and try again. And don’t forget to wash your hands afterward, unless you want to end up with ink-stained fingerprints like a wannabe detective.
EMdigitizing: Embroidery Digitizing Expert At Your Service
If you are interested in any kind of embroidery project, then EMdigitizing is the best option for you. We offer embroidery digitizing and vector art services with a fast turnaround time. You can also visit and check our website as well as our best services.
We also offer a great 50% discount on all our services for our respected first-time clients. We also offer free quotes generated in just 5 minutes.
You should grab this limited-time offer and take your embroidery project to the next level with EMdigitizing.
If you’ve any queries regarding this topic, you can ask them. Thank you for taking the time to read this article.
Frequently Asked Questions:
You need a screen, squeegee, ink, emulsion, a dark room, and a light source for exposure. Additionally, a clean workspace and a drying area for the finished shirts are essential.
Pre-wash the shirt to remove impurities and ensure it’s completely dry before printing. Also, iron the shirt to eliminate any wrinkles that could affect the print quality.
Create your design, prepare and expose the screen, apply ink through the screen onto the shirt, and then cure the ink. Cleaning the screen after use is crucial for future prints.
Yes, with basic equipment and supplies, you can start screen printing at home. Patience and practice are key to achieving professional results.