Quand il s'agit de sérigraphie, le type de maillage que vous utilisez peut grandement affecter le résultat de votre conception. Le maillage de sérigraphie détermine la quantité d'encre qui passe et la finesse des détails de votre conception..
L'utilisation du bon maillage permet de garantir que vos impressions soient claires et éclatantes..Dans ce guide, nous couvrirons les bases des différents types de maillage, comment choisir le bon, et quelques conseils d'entretien simples pour garder vos écrans en bon état.
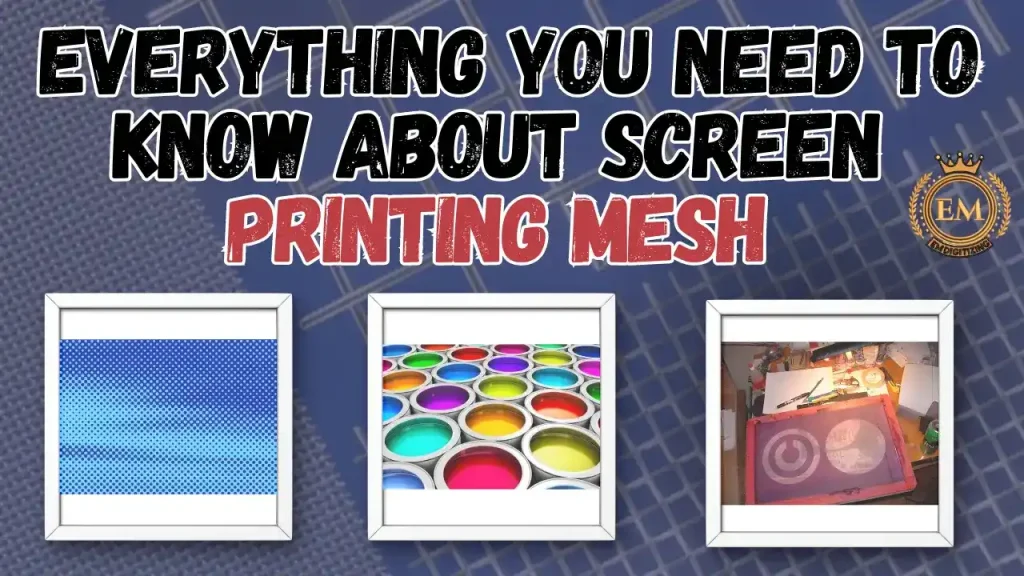
En maîtrisant ces détails, you’;Je pourrai obtenir de meilleurs résultats d'impression.
Tout ce que vous devez savoir sur le maillage de sérigraphie
Qu'est-ce que le maillage de sérigraphie?
C'est un tissu finement tissé qui sert de pochoir dans le impression d'écran processus, utilisé pour transférer de l'encre sur différentes surfaces comme le tissu, papier, verre, et du métal. Il permet à l'encre de passer à travers les zones ouvertes tout en l'empêchant d'atteindre les parties de la surface non destinées à l'impression.. Le maillage est tendu étroitement sur un cadre, et le nombre de mailles et le type de matériau influencent la quantité d'encre appliquée et la précision des détails imprimés..
Quels sont les types de mailles d'écran pour l'impression?
Il en existe de différents types, chacun adapté à différents besoins d'impression en fonction du matériau et du nombre de mailles. Ces différences affectent le dépôt d'encre, détail de l'image, et la qualité d'impression globale.
Les types sont:
- Maille en polyester
- Maille en acier inoxydable
- Maille en nylon
- Maille de soie
1. Maille en polyester
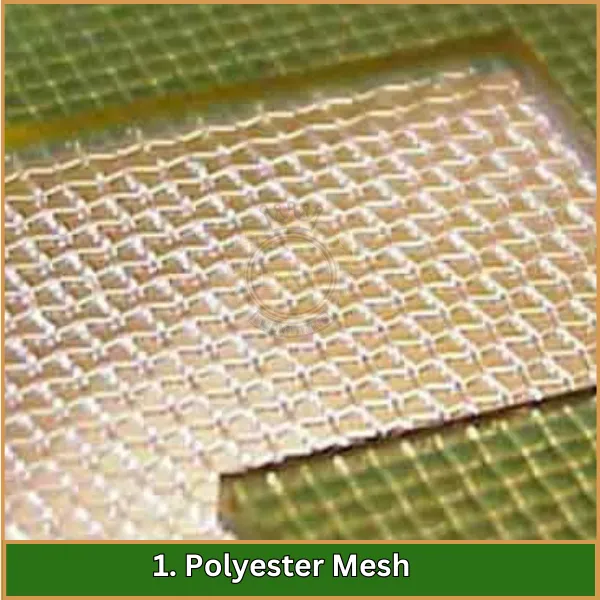
La maille en polyester est un tissu synthétique couramment utilisé dans maille d'écran pour l'impression en raison de sa solidité et de sa résistance chimique.
Principales caractéristiques:
- Haute résistance à la traction et durabilité
- Résistant à la dégradation chimique
Utilisations:
- Idéal pour l'impression sur textiles, céramique, et produits plats ou cylindriques.
Avantages:
- La maille en polyester est abordable et polyvalente, adapté à une variété de travaux d'impression.
Limites:
- Il peut s'étirer davantage sous haute tension, ce qui peut affecter l'enregistrement de l'impression.
2. Maille en acier inoxydable
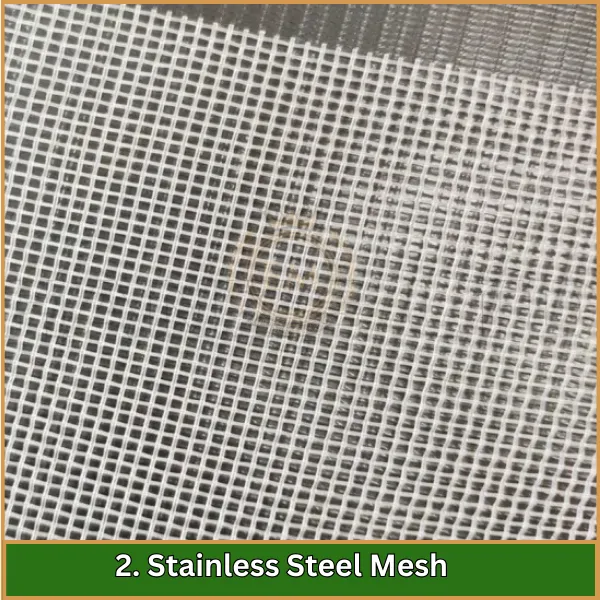
La maille en acier inoxydable est très durable sérigraphie en maille fabriqué à partir de fils métalliques, utilisé pour sa résistance à la chaleur et aux produits chimiques.
Principales caractéristiques:
- Extrêmement durable et solide
- Haute résistance à la chaleur et aux produits chimiques agressifs
Utilisations:
- Utilisé en électronique, impression sur verre, et applications nécessitant un contrôle précis du dépôt d’encre.
Avantages:
- Excellent pour les impressions de haute précision et offre une durabilité supérieure.
Limites:
- Plus cher que les autres types de mailles de sérigraphie.
3. Maille en nylon
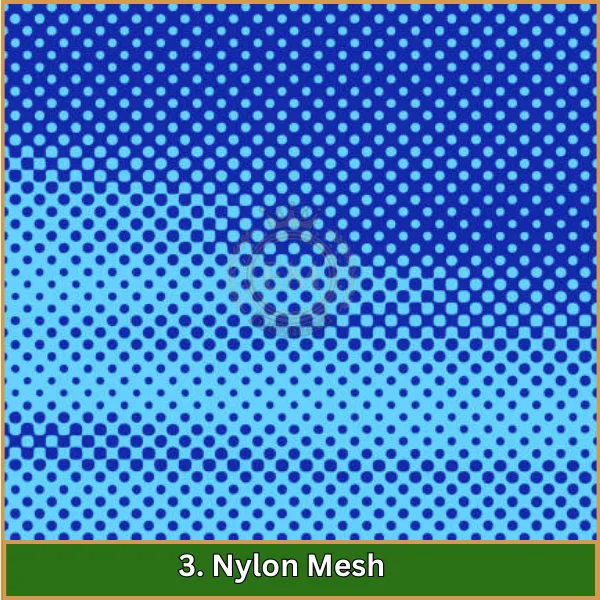
La maille en nylon est un tissu flexible et extensible, privilégié pour son adaptabilité aux surfaces irrégulières.
Principales caractéristiques:
- Haute flexibilité et extensibilité
- Bonne résistance à l'abrasion
Utilisations:
- Convient aux surfaces irrégulières et aux substrats abrasifs comme le verre et la céramique.
Avantages:
- S'adapte bien aux surfaces inégales, offrant plus de polyvalence.
Limites:
- Moins résistant aux solvants que le polyester, ce qui peut limiter son utilisation avec certaines encres.
4. Maille de soie
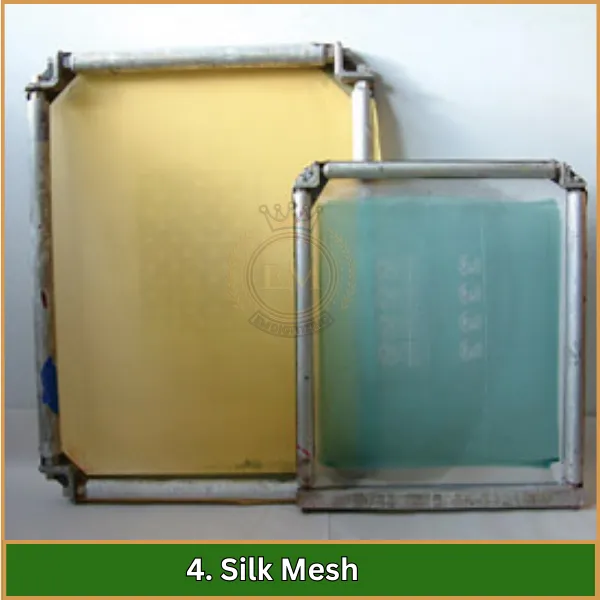
La maille de soie est un matériau traditionnel utilisé dans maille d'écran d'impression pour sa capacité à détailler de belles œuvres d'art, principalement utilisé dans la gravure de haute qualité.
Principales caractéristiques:
- Matériau traditionnel pour la sérigraphie
- Capacité de détails fins
Utilisations:
- Principalement utilisé dans le domaine artistique, impression de haute qualité et applications industrielles limitées.
Avantages:
- Excellent pour créer des œuvres d'art détaillées avec une finition de haute qualité.
Limites:
- Pas aussi durable que les matériaux synthétiques et sensible aux conditions environnementales, nécessitant une manipulation plus prudente.
Qu'est-ce que le nombre de mailles de sérigraphie?
Le nombre de mailles fait référence au nombre de fils par pouce dans un maillage d'impression. Cette mesure est cruciale car elle impacte directement la résolution, dépôt d'encre, et le niveau de détail pouvant être atteint dans le processus d'impression.
Un nombre de mailles plus élevé signifie des fils plus fins et des ouvertures plus petites, qui sont parfaits pour les conceptions détaillées et les fines couches d'encre. inversement, le nombre de mailles inférieur a des ouvertures plus grandes, convient aux encres plus épaisses et aux graphiques plus audacieux.
Types courants de nombre de maillages et leurs applications
Nombre de mailles | Description | Applications courantes |
32T | Faible nombre de mailles, permet un dépôt d'encre plus important, idéal pour les designs audacieux. | Encres spécialisées comme des paillettes ou des flocons. |
43T | Faible nombre de mailles, bon pour les dépôts d'encre importants. | Impression textile avec une excellente couverture. |
55T | Faible nombre de mailles, Couverture et définition des soldes. | Impression textile et applications générales. |
64T | Nombre de mailles moyen, adapté à divers matériaux. | Impression sur textile, papier, et du carton. |
77T | Nombre de mailles moyen, bon pour les détails plus fins. | Vêtements légers et impression sur papier. |
90T | Couramment utilisé pour les conceptions plus détaillées. | Impressions de couche supérieure sur tissu et papier. |
110T | Nombre de mailles polyvalent, adapté aux designs audacieux. | Impression de t-shirts et sérigraphie à usage général. |
156T | Nombre de mailles moyen, équilibre les détails et la couverture d'encre. | Impression textile avec des détails modérés et des couleurs vives. |
230T | Nombre de mailles élevé, idéal pour les détails fins et les encres fines. | Impressions haute résolution sur tissus et papiers plus légers. |
305T | Nombre de mailles très élevé, permet des conceptions complexes. | Illustrations détaillées et demi-teintes sur des surfaces lisses. |
Impact du nombre de maillages sur l'impression
Le nombre de mailles en sérigraphie joue un rôle essentiel dans la détermination de la qualité et des caractéristiques de l'impression finale.. Essentiellement, cela affecte trois aspects majeurs de l’impression: résolution, dépôt d'encre, et la texture de l'impression.
- Résolution: Un nombre de mailles plus élevé, avec plus de fils par pouce, donne un maillage plus fin. Cela permet d'imprimer des détails plus fins car il peut contenir des points d'encre plus petits.. Il est idéal pour les dessins complexes ou les petits textes nécessitant une grande précision..
- Dépôt d'encre: La quantité d'encre qui traverse le maillage jusqu'au substrat varie en fonction du nombre de maillages. Un nombre de mailles inférieur a des ouvertures plus grandes, qui permettent à un plus grand volume d'encre de passer à travers, créant une impression plus dense et plus opaque. Ceci est particulièrement avantageux pour les designs audacieux ou lors de l'utilisation d'encres spéciales comme les encres métalliques ou pailletées..
- Texture de l'impression: La texture de l'impression finale peut également être influencée par le nombre de mailles. Maille plus grossière (nombre de mailles inférieur) donne généralement une couche d'encre plus épaisse, ce qui peut ajouter une texture visible à l'impression. inversement, un nombre de mailles plus élevé permet d'obtenir une couche d'encre plus fine, qui peut être plus doux au toucher.
Ces facteurs contribuent collectivement à la polyvalence des techniques de sérigraphie sur maille., permettant une personnalisation en fonction des besoins spécifiques du travail d'impression, des images artistiques détaillées aux conceptions commerciales robustes.
Considérations relatives à la sélection du maillage de sérigraphie
Lors du choix du bon maillage pour la sérigraphie, plusieurs facteurs doivent être évalués pour garantir une qualité et une efficacité d'impression optimales.
Type de matériau
Le matériau du maillage peut influencer sa durabilité, compatibilité des encres, et qualité d'impression. Les matériaux courants incluent le polyester, nylon, et acier inoxydable, chacun offrant des avantages différents selon l'application d'impression.
Nombre de mailles
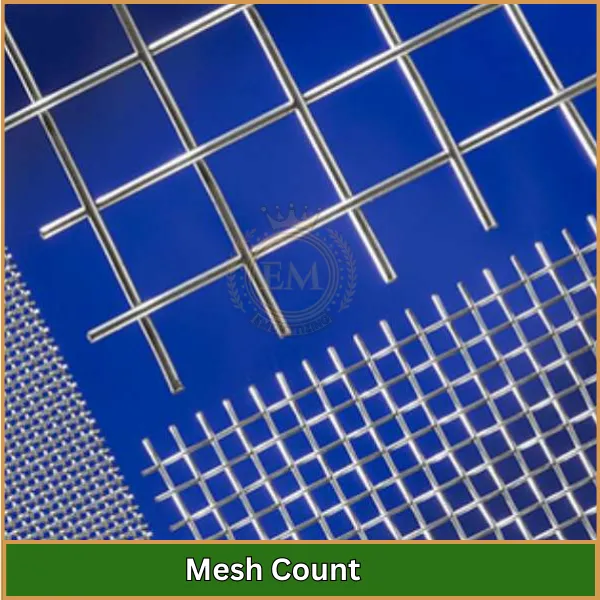
La sélection du nombre de mailles approprié est cruciale car elle affecte la résolution et la quantité d'encre déposée.. Un nombre de mailles plus élevé est utilisé pour des impressions détaillées sur des surfaces lisses, tandis que les comptes inférieurs sont meilleurs pour les impressions en gras sur des surfaces rugueuses.
Diamètre du filetage
Le diamètre des fils dans le maillage peut affecter le dépôt global d'encre et le détail de l'impression.. Des fils plus fins fournissent des impressions détaillées avec moins de dépôt d'encre, adapté aux conceptions très détaillées.
Tension du maillage
Une bonne tension du maillage est essentielle pour éviter des problèmes tels que des impressions floues ou une répartition inégale de l'encre.. Une tension plus élevée entraîne généralement une meilleure qualité d'impression.
Couleur du maillage
La couleur du maillage peut avoir un impact sur les temps d'exposition pendant le processus de fabrication de l'écran et finalement affecter l'impression.. Le maillage blanc offre des temps d'exposition réduits, adapté aux détails les plus fins, tandis que le maillage jaune ou orange permet d'obtenir des images plus nettes et convient mieux aux travaux détaillés très fins..
Conseils d'entretien et de nettoyage pour les mailles de sérigraphie
Pour préserver la qualité et prolonger la durée de vie de votre toile d'impression, un entretien et un nettoyage appropriés sont essentiels. Voici quelques directives simples à suivre:
- Nettoyage régulier: Nettoyez le maillage rapidement après chaque utilisation pour éviter que l'encre ne sèche et n'obstrue les ouvertures du maillage..
- Manipulation douce: Lors du nettoyage, utilisez des brosses douces ou des éponges pour éviter d'endommager les fils du maillage.
- Produits chimiques spécifiques: Choisissez des solutions de nettoyage spécialement conçues pour les mailles, garantissant qu'ils éliminent efficacement l'encre sans endommager le tissu.
- Rinçage minutieux: Rincez toujours soigneusement le maillage avec de l'eau après le nettoyage pour éliminer tout reste de nettoyant ou d'encre..
- Séchage adéquat: Assurez-vous que le filet est complètement sec avant de le ranger dans un endroit propre., zone sèche pour éviter les problèmes de moisissure.
Suivre ces conseils vous aidera à maintenir les performances de votre maillage d'impression et à obtenir des impressions de haute qualité constante..
Conclusion
Choisir le bon maillage de sérigraphie peut faire une grande différence dans la qualité de vos impressions. En comprenant l'impact du maillage sur le flux d'encre et les détails de conception, vous pouvez obtenir plus clair, des résultats plus professionnels. Un entretien et un entretien appropriés contribueront également à prolonger la durée de vie de vos écrans et à conserver une netteté de vos impressions..
Vous cherchez à améliorer vos projets de sérigraphie? Numérisation EM propose un expert services d'art vectoriel conçu pour répondre à vos besoins. Avec des délais d'exécution rapides, prix abordables, et un travail de qualité, nous garantissons que vos créations sont prêtes à être imprimées avec précision. Plus, profiter d'un 50% remise sur votre première commande! Laissez-nous vous aider à faire passer votre impression au niveau supérieur.
FAQ
Oui, tu peux sérigraphie sur un short en maille, mais il est important de bien régler la distance hors contact. L'utilisation d'un matériau de support peut également aider à empêcher l'encre de traverser le maillage..
Le choix du bon nombre de mailles dépend de la complexité du design et du type d'encre.. Un nombre de mailles plus élevé est idéal pour des détails plus fins et des encres plus fines, tandis que les comptes inférieurs fonctionnent mieux pour les designs audacieux et les encres plus épaisses..
Pour nettoyer le maillage de sérigraphie, appliquer un nettoyant pour écran ou un dissolvant d'émulsion, frottez doucement avec une brosse douce pour détacher toute encre ou résidu, puis rincer abondamment à l'eau.
Pour exposer le maillage de sérigraphie, enduire l'écran d'une émulsion photosensible et laisser sécher. Alors, placez votre dessin sur l'écran et exposez-le à une source de lumière UV pendant la durée recommandée, selon votre type d'émulsion.