Have you ever wondered how those vibrant, detailed designs get onto different fabrics? That’s where DTF printing comes in.
Direct to film printing is a fantastic method that allows for the creation of high-quality graphics on a special film, which is then seamlessly transferred onto nearly any fabric type.
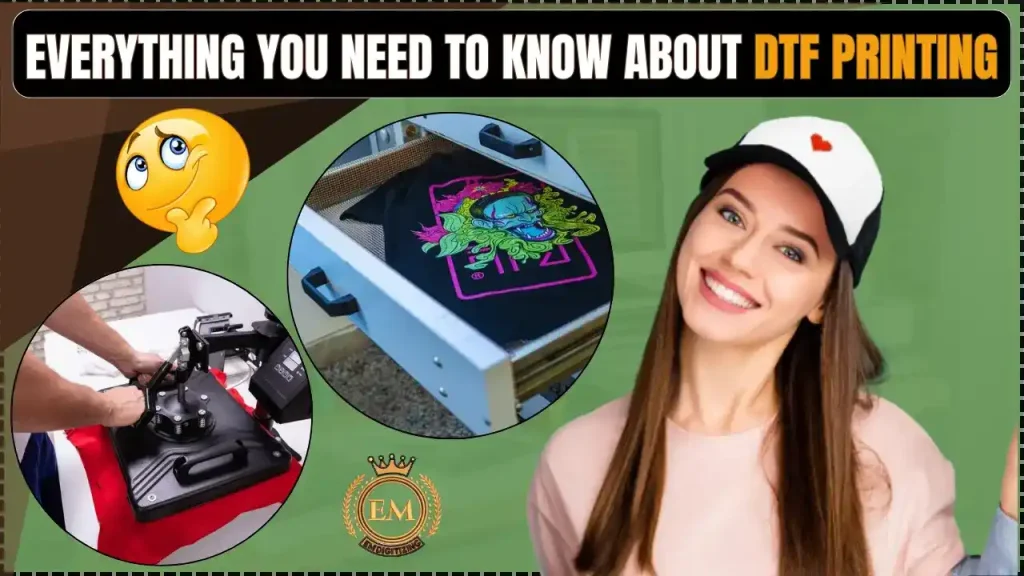
This process is particularly valued for its flexibility, as it does not require any pre-treatment of the fabric, making it suitable for a wide range of applications.
Everything You Need to Know About DTF Printing
Understanding DTF Printing
Direct-to-film technology is a printing method where digital images are first printed onto a special film before being transferred onto fabric. This approach allows for high-resolution and vibrant color reproduction on a variety of textile materials.
How it Works
- Printing on Film: Designs are digitally printed onto a clear, specialized film using specific inks designed for optimal adherence and durability.
- Ink Application: The ink used is formulated to create sharp, vivid images that can adhere well to both the film and the fabric.
- Film Preparation: Once printed, the film undergoes a preparation process where a powder adhesive is applied. This adhesive is key to securing the print onto the fabric.
- Transfer to Fabric: The final step involves transferring the ink from the film to the fabric using heat and pressure, which activates the adhesive and ensures the design adheres firmly to the material.
Advantages and Disadvantages of Direct to Film Printing
It offers a blend of high-quality print capabilities and versatility, making it a favored choice for textile customization. However, it comes with its own set of challenges that can impact its overall efficiency and sustainability.
Let’s explore the benefits and limitations of this innovative printing method.
Advantages:
- Versatility: DTF transfer printing can be applied to a wide range of fabrics, including synthetic blends and delicate materials, without requiring pre-treatment.
- Quality: The ability to print DTF allows for high-resolution, colorful designs that are resistant to fading and cracking, even after multiple washes.
- Cost-Effective: Ideal for small to medium batch sizes, reducing setup costs and waste compared to traditional textile printing methods.
- Customization: This technology supports extensive customization, making it perfect for bespoke fashion and unique promotional items.
Disadvantages:
- Initial Costs: Although print DTF reduces ongoing operational costs, the initial investment in specialized equipment and materials can be high.
- Complexity: Managing the printing process requires technical knowledge and skill, particularly in adjusting printer settings and handling materials.
- Environmental Impact: The use of plastic films and synthetic adhesives poses sustainability concerns, with waste disposal being a significant issue.
- Labor Intensive: The multi-step process, from printing to heat transfer, demands more manual labor compared to direct textile printing methods.
Necessary Tools and Materials for Effective DTF Printing
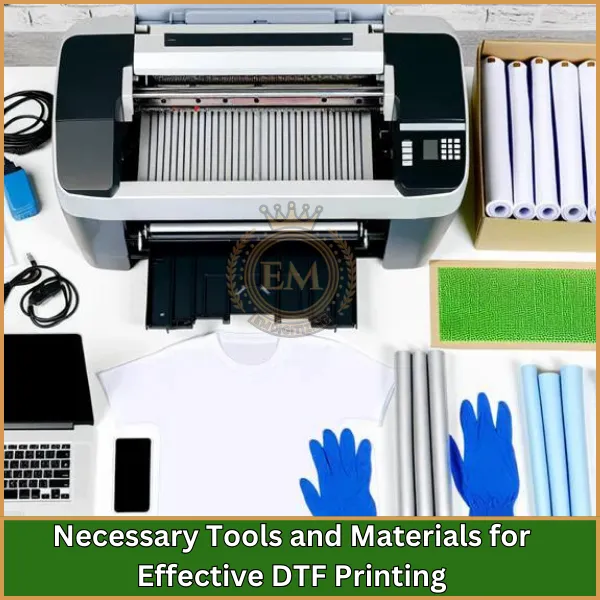
- DTF Printing Machine: A specialized printer capable of handling the unique requirements of film printing.
- Printable Film: Special film sheets designed for transferring printed designs onto textiles.
- DTF Shirt: Pre-prepared shirts optimized for receiving film-transferred designs.
- DTF Inks: Specially formulated inks that adhere to both the film and fabric.
- Powder Adhesive: A crucial component that ensures the design adheres firmly to the fabric after heat pressing.
- Heat Press: Equipment used to apply heat and pressure to transfer the design from the film to the shirt.
7. Shaking Machine: Used to evenly distribute and cure the powder adhesive on the printed film.
8. Curing Oven: Optional but beneficial for setting the ink permanently onto the fabric after transfer.
The Step-by-Step DTF Printing Process
Let’s break down the process of transferring your design onto fabric using direct-to-film technology, step by step.
Step 1: Design Creation
Begin by crafting your graphic using design software tailored for print work.
Step 2: Printing Onto Film
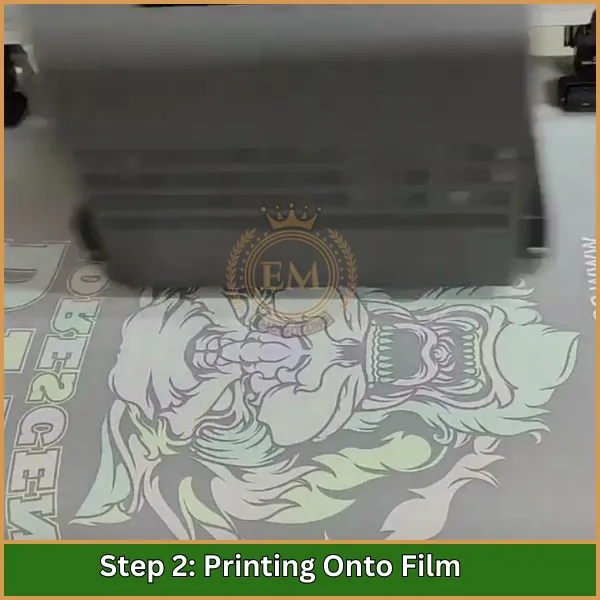
Load the film into a dedicated DTF printer and apply your design directly onto this special substrate.
Step 3: Applying Adhesive Powder
Generously apply a powder adhesive over the freshly printed design; this ensures it will securely bond with the fabric later.
Step 4: Curing the Print
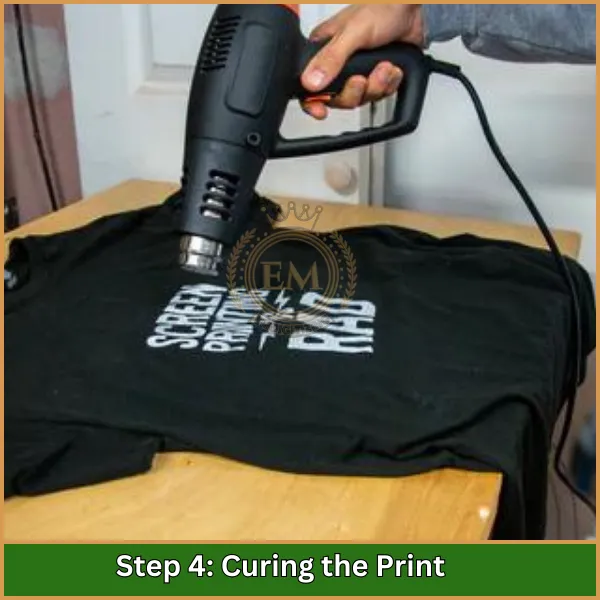
Bake the film in a curing oven or use a heat lamp to dry the adhesive powder onto the design, preparing it for the transfer.
Step 5: Transferring to Fabric
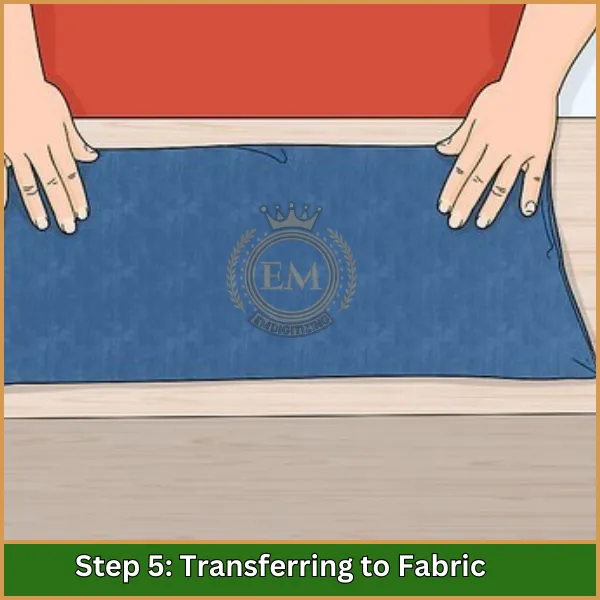
Use a heat press to apply the film onto your fabric. The heat activates the adhesive, bonding the design permanently to the material.
Step 6: Peeling Off the Film
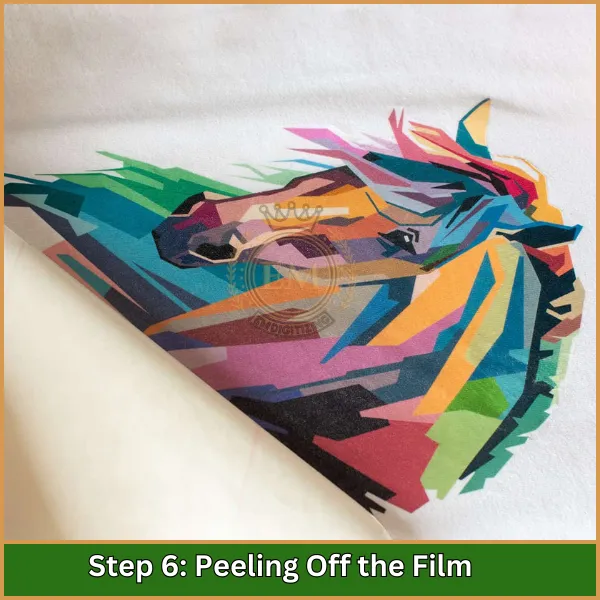
Step 6: Peeling Off the Film
After cooling slightly, carefully remove the film from the fabric, leaving the design intact on the surface.
Step 7: Final Heat Setting
Optionally, you may need to give the fabric a final press under a heat lamp or through a tunnel to fully set the design into the fabric, enhancing its durability and washability.
Troubleshooting Common Issues in DTF Printing
Here’s a handy guide to quickly solving common problems you might face while using the direct-to-film printing method, ensuring your projects turn out perfect every time.
Problem: Ink Not Sticking to Film
- What Happens: The ink fails to adhere to the film properly.
- Quick Fix: Ensure the film is designed for DTF use and double-check your printer settings for optimal ink adhesion.
Problem: Blurry or Faded Prints
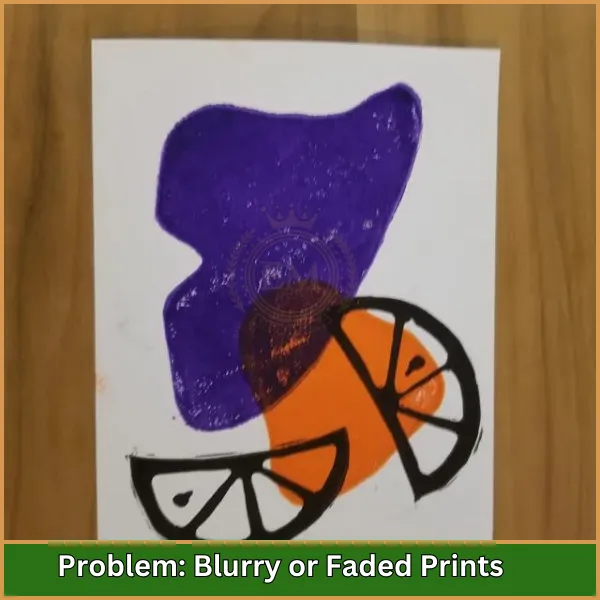
- What Happens: Print quality is compromised, appearing unclear or washed out.
- Quick Fix: Use high-resolution designs, check for adequate ink supply, and clean the printer nozzles to prevent blockages.
Problem: Adhesive Powder Issues
- What Happens: The powder doesn’t stick or fails to activate during the heat transfer.
- Quick Fix: Apply the powder while the ink is wet and make sure it’s evenly distributed with a shaker.
Problem: Inconsistent Color Output
- What Happens: The colors on the fabric look different from the design file.
- Quick Fix: Regularly calibrate your printer and use consistent, high-quality inks.
Problem: Film Peeling During Transfer
- What Happens: The film detaches from the fabric too soon during heat pressing.
- Quick Fix: Adjust your heat press settings to the correct temperature and pressure for the specific materials you’re working with.
Problem: Residual Adhesive on Fabric
- What Happens: There’s sticky residue around the design, affecting fabric feel and comfort.
- Quick Fix: Use less adhesive powder and ensure it is fully cured before pressing to avoid excess sticking to the fabric.
Comparing DTF Transfer Printing with Other Printing Methods
It has become a prominent choice for its versatility and quality, but how does it stack up against other printing techniques?
Let’s compare it with two common methods: DTG (Direct-to-Garment) printing and traditional screen printing.
DTF vs. DTG Printing
- Method: DTF transfers designs from film; DTG prints directly on fabric.
- Fabric Compatibility: DTF works on many fabrics, DTG best on cotton.
- Color Vibrancy: Both offer vibrant colors; DTF has a slightly raised texture.
- Cost Efficiency: DTF is better for small to medium runs.
- Speed: DTF is typically faster in setup and printing multiple items.
DTF vs. Screen Printing
- Method: DTF uses heat transfer; screen printing uses ink through screens.
- Fabric Compatibility: Screen printing excels on more fabrics, including heavy materials.
- Color Vibrancy: Screen printing is highly vibrant with a more textured finish.
- Cost Efficiency: Screen printing is more economical for large orders.
- Speed: Screen printing is quicker for large batches post-setup.
Conclusion
DTF printing is a great way to put designs on clothes and other items. It works well with many types of fabrics and is good for making small to medium batches quickly and easily. DTF makes it easy to create custom designs whenever you need them.
To make your DTF projects even better, try using professional vector art services. At EMdigitizing, we offer high-quality, detailed designs perfect for DTF printing. Our designs help make sure every print looks clear and colorful.
Right now, we’re offering a 50% discount to new customers. Start your DTF printing with EMdigitizing and turn your ideas into beautiful prints that everyone will notice. Let us help you make designs that really grab people’s attention.
FAQs
Yes, DTF printing is durable and lasts through many washes without fading or peeling, making it a reliable option for fabric printing.
It depends. DTF works on more fabrics, including cotton, while sublimation is best for polyester and offers a smooth, dye-like finish.
The main drawbacks are the high initial cost and ongoing expenses for specialized inks and films, plus the process can be complex for beginners.
For small to medium orders, DTF is more cost-effective due to lower setup costs. For large volumes, screen printing may be cheaper.
DTG prints can fade with frequent washing, but proper care can keep them vibrant for a long time.