In questo articolo, Esploreremo i fattori da considerare quando selezioniamo l'inchiostro bianco Wilflex, Comprendi i diversi tipi disponibili, fattori da considerare, approfondire gli effetti e gli additivi speciali, e fornire consigli sulla risoluzione dei problemi.
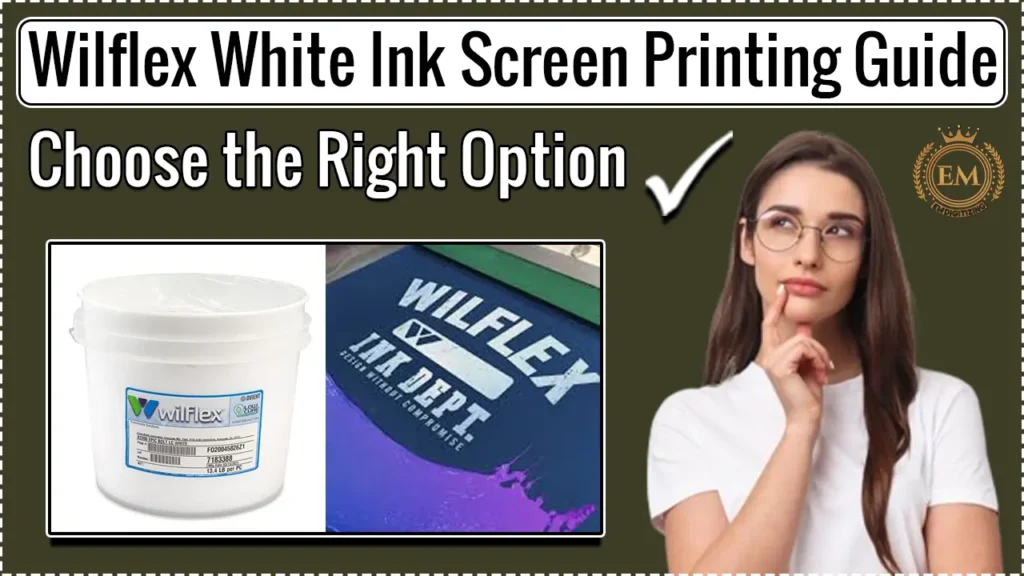
Serigrafia è un metodo versatile e popolare per creare vibranti, design durevoli su vari materiali. Quando si tratta di stampare l'inchiostro bianco, La selezione del prodotto giusto è cruciale per raggiungere i risultati desiderati.
Guida alla stampa serigrafica con inchiostro bianco Wilflex: Scegli l'opzione corretta
Tipi di inchiostri bianchi Wilflex:
Esistono diversi tipi di inchiostri Wilflex disponibili in bianco, quindi discutili uno per uno:
1. Inchiostri a base plastisol:
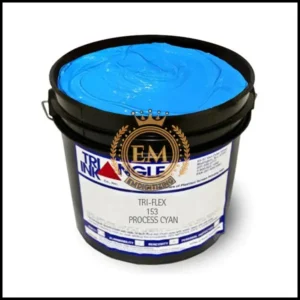
Gli inchiostri Wilflex a base plastisol sono rinomati per la loro facilità d'uso e durata. Ideale per produzioni di grandi volumi, offrono un'eccellente copertura e sono noti per la loro ricchezza, uscita opaca. La loro consistenza più densa è perfetta per le stampe che devono risaltare.
2. Inchiostri a base acqua:
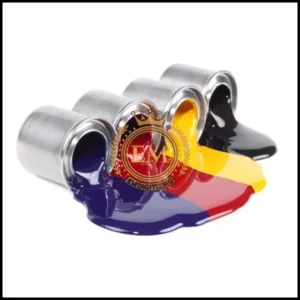
Gli inchiostri a base acqua di Wilflex offrono una sensazione più morbida al tatto e sono più rispettosi dell'ambiente. Questi inchiostri vengono assorbiti maggiormente nel tessuto, garantendo una stampa più integrata con il capo. Sono particolarmente adatti per tessuti leggeri.
3. Inchiostri bianchi speciali:
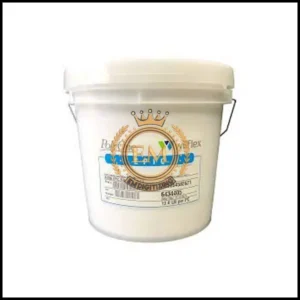
Wilflex fornisce anche inchiostri bianchi speciali per applicazioni uniche, come i tessuti ad alta elasticità, o per creare effetti specifici come stampe fosforescenti. Questi inchiostri specializzati consentono agli stampatori di ampliare i confini della serigrafia convenzionale.
Fattori da considerare quando si seleziona l'inchiostro bianco Wilflex
Diamo un'occhiata alle cose che devi considerare quando selezioni gli inchiostri bianchi:
Opacità e luminosità:
L'opacità dell'inchiostro è fondamentale per stampe chiare e vivide. Gli inchiostri bianchi di Wilflex sono progettati per massimizzare la luminosità, garantendo un puro, aspetto bianco intenso su vari tessuti.
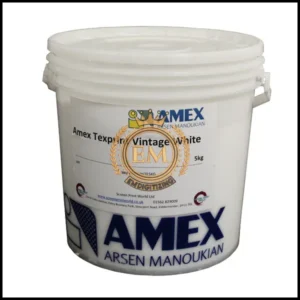
Gli inchiostri plastisol offrono generalmente una migliore opacità rispetto agli inchiostri a base acqua, realizzandoli ideale per la stampa su tessuti scuri dove è richiesta un'elevata copertura. Gli inchiostri a base solvente possono anche fornire un'eccellente coprenza su superfici non porose.
Compatibilità del tessuto:
Inchiostri diversi reagiscono in modo diverso su tessuti diversi. Selecting an ink that aligns with the fabric’;Le sue proprietà sono essenziali per ottenere risultati ottimali. Wilflex offre formulazioni specifiche per diverse tipologie di tessuto, dal cotone ai sintetici.
Proprietà di polimerizzazione ed essiccazione:
Una corretta polimerizzazione è vitale per la longevità e la durata della stampa. Ogni inchiostro Wilflex ha requisiti di polimerizzazione specifici, e seguendo queste linee guida è fondamentale per prevenire problemi come screpolature o scolorimento.
Tecnica di stampa:
Anche la tecnica di stampa scelta gioca un ruolo nella scelta dell'inchiostro bianco ideale. Gli inchiostri a base acqua sono adatti per i metodi di stampa manuale, mentre gli inchiostri plastisol funzionano bene sia con macchine da stampa manuali che automatiche.
Gli inchiostri a base solvente sono comunemente usati per applicazioni industriali e richiedono attrezzature specializzate.
Finitura ed effetti desiderati:
Considera la finitura e gli effetti desiderati che desideri ottenere con le tue stampe. Gli inchiostri a base d'acqua offrono un aspetto più morbido e naturale, Mentre gli inchiostri di plastisolo forniscono una finitura lucida e vibrante. Gli inchiostri a base di solventi sono noti per la loro durata e resistenza allo sbiadimento.
Selezione dell'inchiostro bianco Wilflex giusto per diversi tipi di tessuto:
Quali tipi di inchiostro puoi usare per il tessuto, Discutiamo di loro:
Cotone e miscele:
Le miscele di cotone e cotone sono i tessuti più comuni nella stampa dello schermo. La selezione di un inchiostro che penetra bene in queste fibre garantisce una stampa duratura.
Tessuti sintetici:
I materiali sintetici richiedono inchiostri che possono aderire bene alle loro superfici. Gli inchiostri Wilflex progettati per i sintetici hanno spesso diversi tempi di indurimento e temperature per ospitare le proprietà uniche di questi tessuti.
Tessuti scuri vs leggeri:
La stampa su tessuti scuri richiede in genere una base bianca precisione del colore. La scelta dell'inchiostro bianco per questo scopo è fondamentale per garantire che i colori superiori rimangano vibranti e fedeli alle tonalità.
Tecniche di applicazione degli inchiostri bianchi Wilflex:
Quando si utilizzano gli inchiostri Wilflex è necessario seguire alcune tecniche:
Selezione della mesh dello schermo:
La scelta del retino influisce in modo significativo sulla qualità di stampa finale. Una mesh più fine viene generalmente utilizzata per progetti dettagliati, mentre una maglia più grossa è migliore per i più audaci, stampe meno complesse.
Tecniche di spatola:
The squeegee’;s angolo, pressione, e la velocità svolgono un ruolo fondamentale nell'applicazione dell'inchiostro. Padroneggiare queste tecniche è fondamentale per ottenere stampe uniformi e coerenti.
Stratificazione e polimerizzazione flash:
La sovrapposizione di inchiostri diversi e l'utilizzo di tecniche di essiccazione rapida possono creare effetti dinamici e strutturati. Comprendere come interagire inchiostri diversi è cruciale per la stratificazione di successo.
Esplorare effetti e additivi speciali negli inchiostri bianchi Wilflex:
Puoi aggiungere diversi effetti nella stampa sullo schermo con i loro inchiostri come:
Effetti metallici e luccicanti:
Chi dice che le tue stampe devono essere ordinarie?
Con inchiostri bianchi Wilflex, Puoi aggiungere un tocco di magia ai tuoi disegni con effetti metallici e luccicanti. Whether you’;Stai cercando un look futuristico o vuoi far brillare le tue stampe come una palla da discoteca, Questi effetti speciali eleneranno le tue creazioni a un livello completamente nuovo.
Effetti bagliore e fluorescenti:
Voglio far illuminare le tue stampe la notte?
Gli inchiostri bianchi di Wilflex offrono effetti di bagliore e fluorescenti che faranno scoppiare i tuoi progetti, anche nelle stanze più scure. Whether it’;Ideale per un design spettrale di Halloween o un evento a tema neon, questi additivi garantiranno che le tue stampe rubino la scena.
Additivi per una maggiore elasticità o morbidezza:
La comodità è fondamentale, soprattutto quando si tratta di abbigliamento. That’;Ecco perché gli inchiostri bianchi Wilflex offrono additivi che migliorano l'elasticità e la morbidezza delle tue stampe.
Whether you’;stai stampando su capi di abbigliamento da prestazione o desideri semplicemente un'atmosfera accogliente, questi additivi garantiranno che le tue stampe non solo abbiano un bell'aspetto ma anche una sensazione straordinaria sulla pelle.
Risoluzione dei problemi comuni con gli inchiostri bianchi Wilflex:
Serigrafia, come la vita, non è sempre una navigazione tranquilla.
Ma non temere!
Perché abbiamo alcuni suggerimenti utili per la risoluzione dei problemi per salvare la situazione. Dall'asciugatura troppo rapida dell'inchiostro alle stampe irregolari, we’;Ti abbiamo fornito soluzioni pratiche alle sfide comuni.
Così, don’;Non lasciare che un ostacolo sulla strada rovini le tue avventure di stampa!
Problemi di spessore e copertura dell'inchiostro:
L'obiettivo sono le stampe opache, ma a volte ottenere una copertura così solida può sembrare un gioco a nascondino. Se le tue stampe mancano di opacità, try adjusting your ink’;s viscosità e aumento del numero di strati.
Puoi anche sperimentare diversi conteggi di mesh e tensione dello schermo per trovare la combinazione perfetta per una copertura impeccabile.
Problemi di polimerizzazione e lavabilità:
Una polimerizzazione non corretta può compromettere la lavabilità della stampa. Garantire che l'inchiostro si asciughi alla giusta temperatura e durata è fondamentale per mantenere la qualità di stampa.
Precisione del colore e sbavatura:
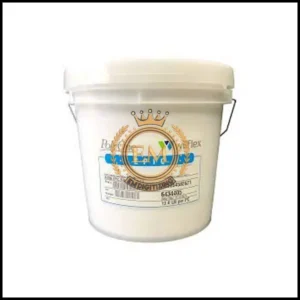
Wilflex fornisce anche inchiostri bianchi speciali per applicazioni uniche, come i tessuti ad alta elasticità, o per creare effetti specifici come stampe fosforescenti. Questi inchiostri specializzati consentono agli stampatori di ampliare i confini della serigrafia convenzionale.
Verdetto finale:
Selezionare il miglior inchiostro bianco Wilflex per i tuoi lavori di serigrafia è molto importante per ottenere buoni risultati, risultati duraturi. Think about the kind of fabric you’;stai usando, il suo colore e l'effetto che vuoi ottenere quando scegli l'inchiostro.
Use the tips we’;VE ha condiviso e risolto eventuali problemi che emergono. Con l'inchiostro bianco giusto e alcune strategie intelligenti, you’;sarà stampato come un esperto molto presto!
Domande frequenti:
Wilflex White Ink è essenziale per la stampa dello schermo grazie alla sua alta opacità e qualità, Garantire stampe chiare e vibranti su vari tessuti.
La durata di conservazione dell'inchiostro Wilflex è di circa un anno, and it’;è meglio immagazzinato in una bella, ambiente secco, schermato dalla luce solare diretta e temperature estreme.
È formulato pensando alla sicurezza ambientale, Ma lo smaltimento adeguato e l'adesione ai protocolli di sicurezza sono necessari per l'uso ecologico.
Per garantire correttamente le cure di inchiostro bianco Wilflex, Seguire le impostazioni specifiche del tempo e della temperatura, In genere utilizzando apparecchiature specializzate come una pressa di calore o un asciugatrice.