Vous êtes-vous déjà demandé, "Qu'est-ce que la sérigraphie?" C'est une façon amusante et créative d'imprimer des motifs sur des matériaux comme le tissu., papier, et plus. Cette technique fonctionne en utilisant un pochoir sur un écran à mailles pour transférer l'encre., donner vie à vos idées.
La sérigraphie est largement appréciée pour ses couleurs vives et ses résultats durables., c'est pourquoi il est souvent utilisé pour les T-shirts personnalisés, affiches, et autres objets uniques.
Dans ce guide, nous vous guiderons tout au long du processus en étapes simples. Que vous débutiez en sérigraphie ou que vous souhaitiez améliorer vos compétences, ce guide vous aidera à comprendre les bases et à démarrer votre propre projet d'impression. Plongeons dedans!

Qu'est-ce que la sérigraphie? Un guide complet
Comprendre la sérigraphie
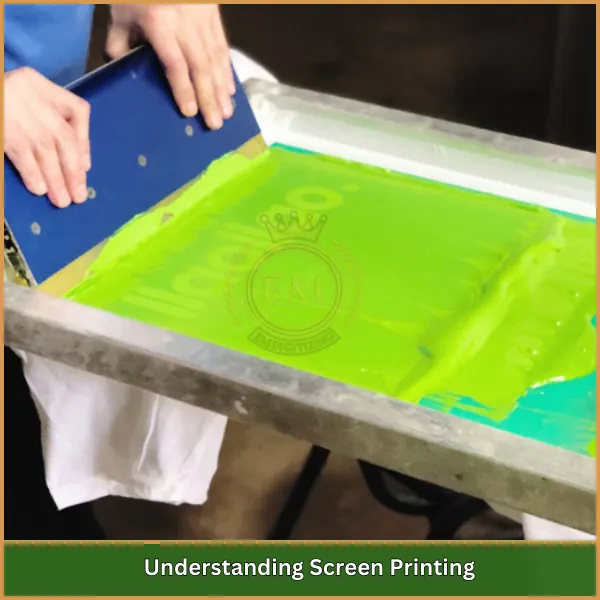
Impression d'écran, souvent appelé sérigraphie, est une méthode où l'encre est soigneusement transférée à travers un tamis qui contient un pochoir. Ce processus donne vie à des conceptions complexes sur une large gamme de matériaux, y compris le tissu, papier, plastique, et même du verre. C'est une technique polyvalente et créative utilisée pour créer des impressions détaillées sur diverses surfaces..
Types de techniques de sérigraphie
Impression d'écran est une forme d'art polyvalente avec de nombreux types de sérigraphie qui répondent à différents besoins et visions créatives.. Chaque méthode est unique dans son processus et les résultats qu'elle fournit, offrant des possibilités infinies de personnalisation sur divers matériaux.
- Sérigraphie traditionnelle: Cette méthode classique utilise un tamis et un pochoir pour transférer l'encre sur des matériaux comme le tissu., papier, ou en plastique. C’est une technique incontournable pour des designs nets et précis.
- Sérigraphie à base d'eau: Un choix éco-responsable, cette méthode utilise des encres à base d'eau qui pénètrent dans les tissus, créer du doux, imprimés respirants parfaits pour les vêtements.
- Sérigraphie de décharge: Idéal pour les tissus foncés, cette méthode utilise un agent de décharge pour éliminer le colorant du matériau, résultant en dynamique, dessins à effet blanchi.
- Sérigraphie Plastisol: Connu pour ses couleurs vives et sa longévité, Les encres plastisol reposent sur le matériau et sont durcies à chaud pour garantir la durabilité..
- Sérigraphie métallique: Cette méthode utilise des encres métalliques pour ajouter un effet réfléchissant, finition brillante, souvent utilisé pour faire ressortir les vêtements et les articles promotionnels.
- Sérigraphie UV: Conçu pour un séchage rapide et des résultats de haute qualité, cette technique utilise des encres durcissables aux UV qui durcissent sous la lumière ultraviolette, adapté au verre, métal, et surfaces en plastique.
- Sérigraphie haute densité: Pour un effet 3D, d'épaisses couches d'encre sont appliquées pour créer des motifs en relief, ajouter de la texture et de la dimension à l'impression.
- Sérigraphie intégrale: Également appelée impression géante, cette technique permet des conceptions à couverture complète, ce qui le rend idéal pour les imprimés audacieux sur de grands vêtements comme les T-shirts et les sweats à capuche.
Qu'est-ce que la sérigraphie; c'est plus qu'une simple méthode d'impression; c'est un outil polyvalent pour créer des effets saisissants, dessins personnalisés. Chaque technique offre une manière unique d'explorer ce que la sérigraphie peut réaliser, des détails complexes aux audacieux, motifs all-over.
Matériaux et outils nécessaires à la sérigraphie
Les outils de sérigraphie sont l’épine dorsale de ce processus créatif, s'assurer que chaque étape est fluide et précise. De la préparation de l'écran au durcissement du design final, avoir les bons outils est essentiel pour réussir.
- Écran à mailles
- Raclette
- Émulsion photo
- Unité d'exposition
- Dissolvant d'émulsion
- Station de lavage
- Encres d'imprimerie
- Substrats
- Logiciel de conception graphique
- Ruban de dépistage
- Équipement de durcissement thermique
- Équipement d'enregistrement
- Brosses et chiffons de nettoyage
- Film transparent ou pochoir
1. Écran à mailles
L'épine dorsale de la sérigraphie, un tamis à mailles est tendu étroitement sur un cadre, servant de base au transfert de l'encre sur le substrat.
2. Raclette
Un outil indispensable avec une lame plate en caoutchouc, la raclette répartit l'encre uniformément sur l'écran, en le pressant à travers le maillage pour créer le motif.
3. Émulsion photo
Ce liquide sensible à la lumière est appliqué sur le tamis pour créer un pochoir.. Lorsqu'il est exposé à la lumière, il durcit dans des zones spécifiques, laisser le dessin prêt à être imprimé.
4. Unité d'exposition
Cet appareil utilise la lumière UV pour exposer l'écran enduit d'émulsion, solidifier les zones non couvertes par la conception, former un pochoir précis.
5. Dissolvant d'émulsion
Une solution chimique qui aide à nettoyer la photo-émulsion de l'écran après utilisation, rendre l'écran réutilisable pour de nouveaux designs.
6. Station de lavage
Un espace équipé d'outils à eau sous pression pour rincer et nettoyer l'écran après exposition, s'assurer que le design est clairement visible et prêt à être imprimé.
7. Encres d'imprimerie
Des encres de sérigraphie spécialement formulées comme le plastisol ou à base d'eau sont utilisées pour donner vie aux designs.. Chaque type offre des avantages uniques, comme les couleurs vives ou le respect de l'environnement.
8. Substrats
Ce sont les matériaux sur lesquels les dessins sont imprimés, y compris le tissu, papier, métal, bois, ou en plastique, selon les exigences du projet.
9. Logiciel de conception graphique
Des programmes comme Adobe Illustrator ou CorelDRAW sont essentiels pour créer et éditer les illustrations à transférer sur l'écran..
10. Ruban de dépistage
Utilisé pour bloquer les zones indésirables sur l'écran, le ruban de tramage garantit que l'encre ne passe qu'à travers les parties du maillage destinées au motif.
11. Équipement de durcissement thermique
Après l'impression, un équipement de durcissement tel qu'un séchoir flash ou une presse à chaud est nécessaire pour fixer l'encre, assurant durabilité et résistance à l’usure.
12. Équipement d'enregistrement
Ces outils garantissent que plusieurs écrans s'alignent parfaitement pour impressions multicolores, maintenir l'exactitude et la précision de la conception.
13. Brosses et chiffons de nettoyage
Pour l'entretien et le nettoyage, les brosses et les chiffons sont indispensables pour maintenir les écrans, raclettes, et espaces de travail en excellent état.
14. Film transparent ou pochoir
Utilisé pour créer des pochoirs, ce film bloque la lumière dans des zones spécifiques pendant l'exposition, garantir que le design soit transféré avec précision sur l'écran.
Qu'est-ce que la sérigraphie: Guide étape par étape
La sérigraphie est un processus créatif qui transforme les designs en impressions de haute qualité. Chaque étape joue un rôle crucial pour obtenir un résultat impeccable. Plongeons dans le processus:
Marcher 1: Création de l'œuvre d'art
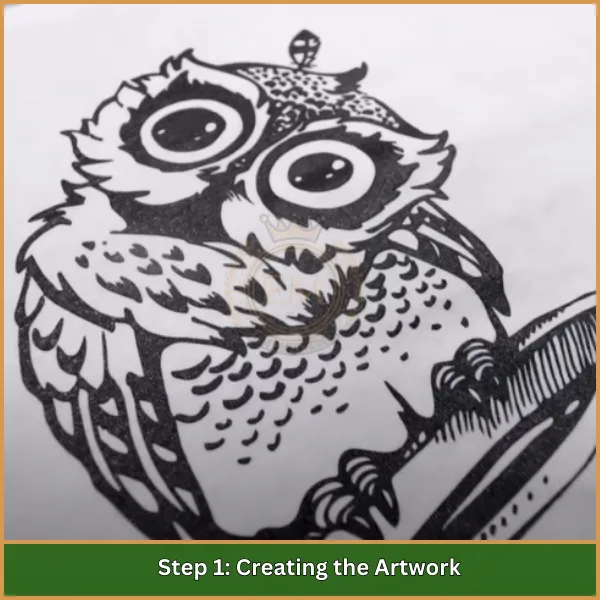
Le voyage commence par la conception de l'œuvre d'art. Un logiciel de conception graphique est utilisé pour créer l'image, qui est ensuite imprimé sur un film transparent qui fait office de pochoir.
Marcher 2: Préparation de l'écran
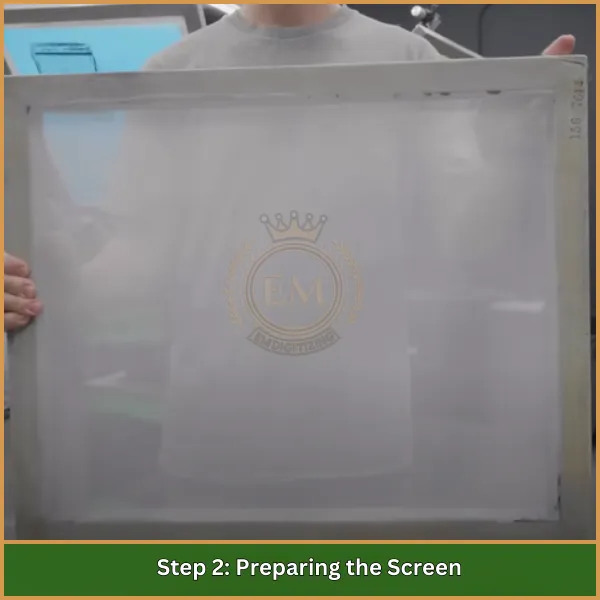
Un tamis maillé est choisi en fonction des besoins du projet. Il est recouvert d'une couche d'émulsion photosensible, qui prépare le terrain pour la création du pochoir.
Marcher 3: Exposer le design

Le film transparent avec le dessin est placé sur l'écran enduit d'émulsion. L'exposition aux rayons UV durcit l'émulsion dans les zones non couvertes, laissant les parties du motif douces.
Marcher 4: Rinçage de l'écran

Après l'exposition, l'écran est lavé à l'eau pour éliminer l'émulsion ramollie. Cette étape révèle le pochoir, ce qui permettra à l'encre de passer au travers lors de l'impression.
Marcher 5: Configuration de l'équipement
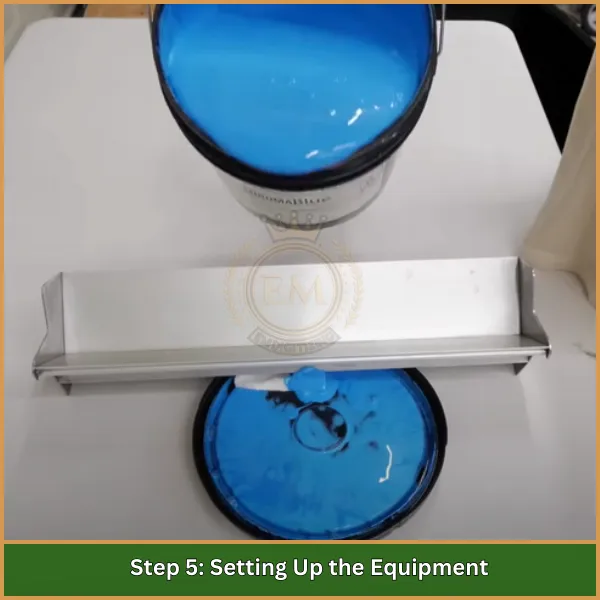
L'écran est solidement placé sur une presse à imprimer, et le matériel (en tissu, papier, etc.) est aligné en dessous. Une configuration appropriée est essentielle pour garantir une impression précise.
Marcher 6: Application de l'encre
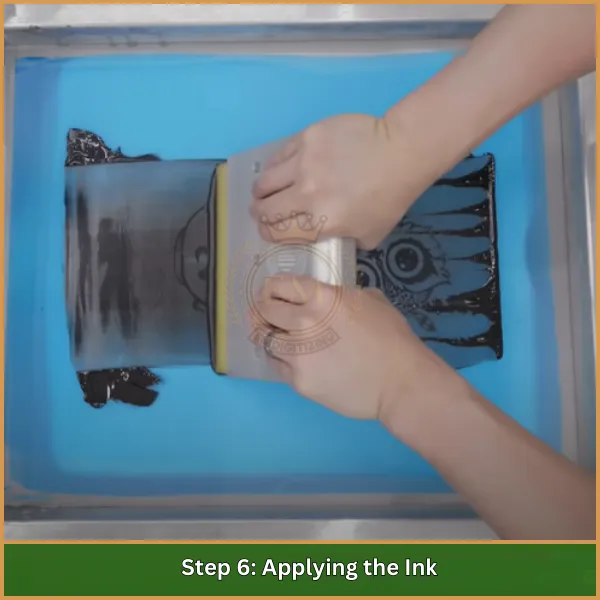
L'encre est versée à une extrémité de l'écran, et une raclette est utilisée pour le pousser uniformément sur le pochoir. L'encre est transférée à travers les zones ouvertes, donner vie au design sur le matériau.
Marcher 7: Séchage et finalisation
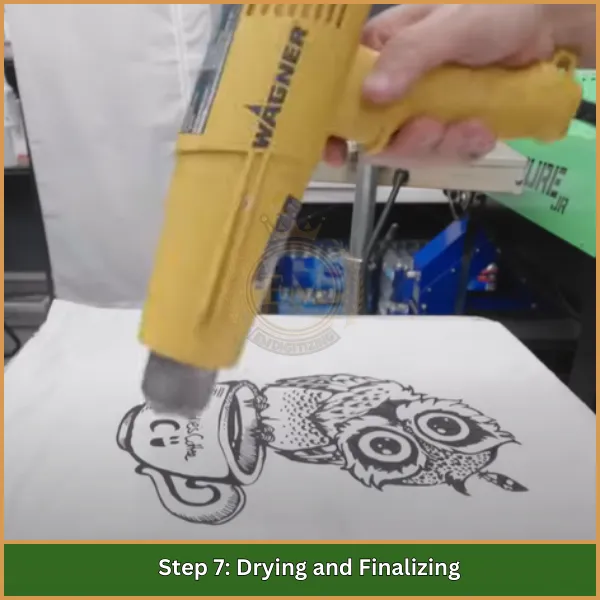
L'article imprimé est déplacé vers une station de durcissement où la chaleur est appliquée pour sécher et fixer l'encre.. Cela garantit que la conception est durable et résistante à l'usure. Après un contrôle qualité, le produit est prêt à être utilisé ou distribué.
Conseils essentiels pour une sérigraphie réussie
- Gardez votre espace de travail propre: Un environnement sans poussière garantit que vos impressions seront nettes et impeccables, minimiser les erreurs.
- Utilisez des pochoirs de qualité: Des pochoirs bien préparés avec une couche d'émulsion lisse donnent des résultats nets., conceptions professionnelles.
- Choisissez le bon nombre de mailles: Match the screen mesh to your design’;le détail. Utilisez des comptes inférieurs pour les encres épaisses et des comptes plus élevés pour les motifs complexes.
- Alignez parfaitement les écrans: Un enregistrement correct est crucial pour les impressions multicolores. Assurez-vous que tous les écrans sont alignés pour éviter les chevauchements ou les conceptions mal alignées..
- Mélangez soigneusement les encres: Les encres constamment mélangées offrent une couleur uniforme et une application fluide., améliorer la qualité globale.
- Traitement flash entre les couleurs: Durcir brièvement chaque couleur évite les bavures et assure une propreté, look superposé pour des impressions multicolores.
- Guérir les impressions correctement: Un durcissement thermique approprié améliore la durabilité et empêche les impressions de se décolorer ou de se fissurer.
- Effectuer un test d'impression: Vérifiez toujours un test d'impression pour détecter les problèmes avant de démarrer la production complète..
Conclusion
Vous savez maintenant ce qu'est la sérigraphie et comment elle donne vie aux motifs sur le tissu., papier, et plus. C’est un processus créatif que tout le monde peut maîtriser avec les bons outils et techniques.
Pour rendre vos projets de sérigraphie encore plus faciles, Numérisation EM est là pour aider! Nous proposons des services professionnels d’art vectoriel aux meilleurs prix, assurant une livraison rapide et une qualité inégalée. Plus, vous pouvez prévisualiser votre conception avant qu'elle ne soit finalisée, donc tu sais exactement à quoi t'attendre.
Si vous nous essayez pour la première fois, voici une offre exclusive: Obtenir 50% désactivé votre première commande! Que vous démarriez un nouveau projet ou que vous ayez besoin des conceptions de haute qualité, EMdigitizing est votre partenaire de confiance.
FAQ
La sérigraphie est une technique classique où l'encre est pressée à travers un écran maillé pour créer des motifs détaillés sur diverses surfaces comme le tissu., papier, et du plastique.
La sérigraphie sur des T-shirts consiste à utiliser un pochoir et un écran à mailles pour transférer l'encre sur le tissu., résultant en des designs dynamiques et durables.
Pour la sérigraphie de T-shirts, vous aurez besoin d'éléments comme un écran maillé, pochoir, raclette, encres d'imprimerie, et un dispositif de durcissement. Des outils supplémentaires comme l’émulsion et les produits de nettoyage sont également utiles.
Les techniques de sérigraphie incluent les techniques traditionnelles, à base d'eau, décharge, plastisol, métallique, Impression UV, et plus, chacun offrant des résultats uniques pour diverses applications.